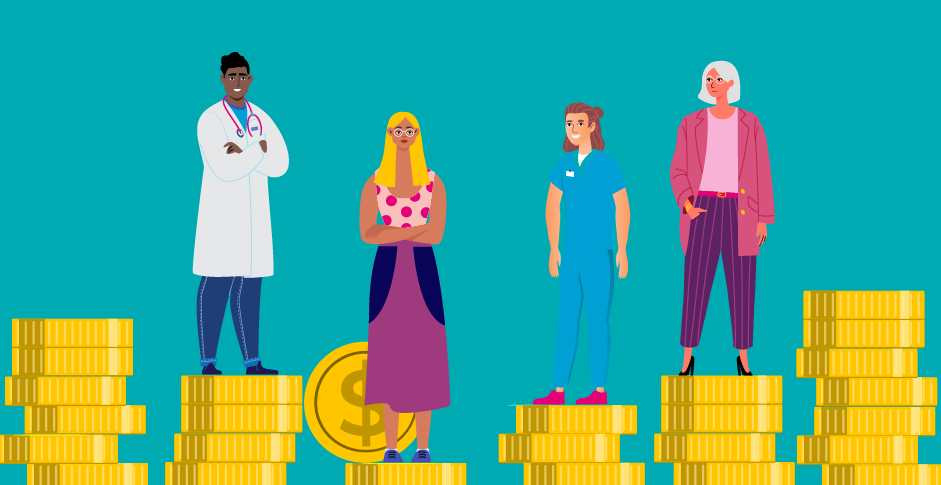
It is important that you include all the duties in the job description to attract the best people for transport and logistic jobs. These duties can include filling company paperwork and ordering raw materials. While leaving out these duties from the job description will make the vacancy sound more appealing, it can also result in hiring the wrong person. This can be a problem for both your business and your customers. It can also mean that you need to spend time and money training new employees.
Job description
Many industries employ transport and logistics professionals to move people or goods from one point to another. Some professionals work in shipping. Others may be involved with road maintenance. Monitoring traffic congestion and product safety is part of the job. Those who work in this field are often required to adapt to changing business needs and work in various locations.
An effective job description is designed to focus on the specific skills and training necessary for a specific job, while also reflecting the company's culture and values. It should indicate whether the job is permanent, interim, or self-employed.
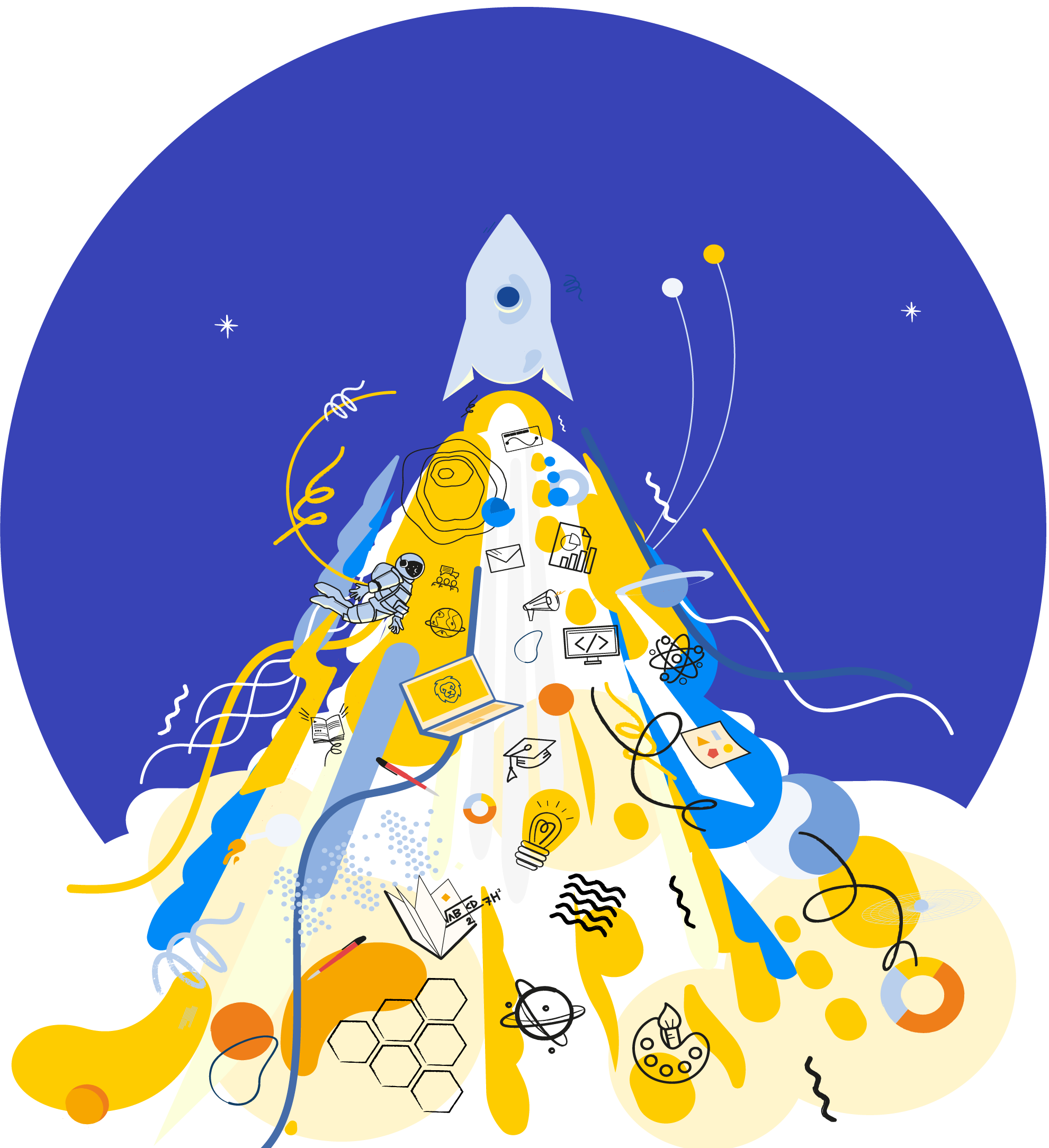
Salary
There are many opportunities for transport and logistics jobs, from entry-level to senior positions. The industry you work in and your experience will determine the salary level. Entry-level positions usually start around $40,000 per year. These salaries are not guaranteed to be the highest, but there is always room for growth.
There are many salary options for logistics and transportation careers, some more lucrative than others. Although entry-level wages may not be as high as those in other fields of work, experienced workers may make much more. Some companies offer in-house training or even pay for graduate-level education.
Requirements
High-skilled workers in logistics and transportation are highly sought after by many industries. These jobs focus on ensuring that goods are delivered safely, promptly, and at the best possible price. It is crucial for companies to hire the right employees with the right skills. Although junior staff may not need training, they should have the qualifications to become a Supply Chain Practitioner Advanced Apprenticeship. Chartered Institute of Logistics and Transport accredited certifications are also required for those seeking senior positions.
If you are considering a career in transport and logistics, a good degree is the first step. You can take many courses to increase your skills and knowledge. The Chartered Institute of Logistics and Transport (CILT) UK offers a Level 2 Certificate in Transport and Logistics, which is ideal for new entrants to the field. You can also gain valuable work experience by undertaking a graduate recruitment scheme, which is offered by many large logistics companies.
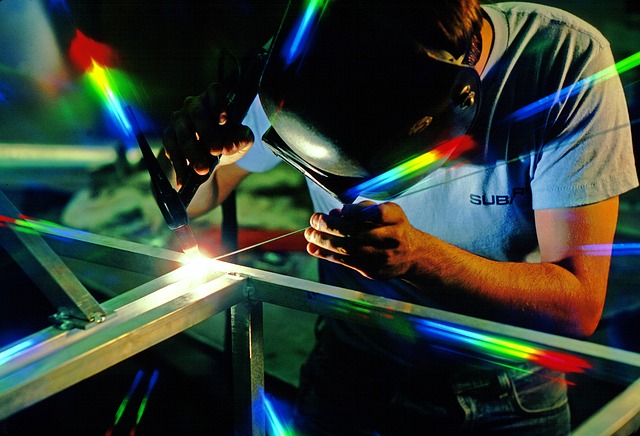
Localities
Careers in transport and logistics are very varied. Many of these jobs require the ability to plan and evaluate different distribution methods. These jobs require analytical thinking and the ability of managing complex data. You must also have excellent communication skills. Some jobs require you travel to remote places. Graduate training schemes in transport and logistics are available, and they provide you with the skills needed to succeed in the field. Some programs offer internships that are paid.
Transportation and logistics occupations are in high demand and are expected to grow 3% from 2019 to 2029, on par with the national average. However, some occupations are expected to grow faster than average such as those that require commercial pilots or airline pilots. Other jobs in this sector include driver/sales workers and delivery truck drivers.
FAQ
What makes a production planner different from a project manger?
The main difference between a production planner and a project manager is that a project manager is usually the person who plans and organizes the entire project, whereas a production planner is mainly involved in the planning stage of the project.
What are the responsibilities of a logistic manager?
A logistics manager makes sure that all goods are delivered on-time and in good condition. This is done using his/her knowledge of the company's products. He/she must also ensure sufficient stock to meet the demand.
What are the jobs in logistics?
Logistics can offer many different jobs. Some of them are:
-
Warehouse workers - They load and unload trucks and pallets.
-
Transportation drivers – These drivers drive trucks and wagons to transport goods and pick up the goods.
-
Freight handlers - They sort and pack freight in warehouses.
-
Inventory managers – They manage the inventory in warehouses.
-
Sales representatives - They sell products to customers.
-
Logistics coordinators: They plan and manage logistics operations.
-
Purchasing agents are those who purchase goods and services for the company.
-
Customer service representatives are available to answer customer calls and emails.
-
Shipping clerks - They process shipping orders and issue bills.
-
Order fillers: They fill orders based off what has been ordered and shipped.
-
Quality control inspectors – They inspect incoming and outgoing products to ensure that there are no defects.
-
Others - There are many types of jobs in logistics such as transport supervisors and cargo specialists.
Statistics
- (2:04) MTO is a production technique wherein products are customized according to customer specifications, and production only starts after an order is received. (oracle.com)
- [54][55] These are the top 50 countries by the total value of manufacturing output in US dollars for its noted year according to World Bank.[56] (en.wikipedia.org)
- In 2021, an estimated 12.1 million Americans work in the manufacturing sector.6 (investopedia.com)
- Job #1 is delivering the ordered product according to specifications: color, size, brand, and quantity. (netsuite.com)
- Many factories witnessed a 30% increase in output due to the shift to electric motors. (en.wikipedia.org)
External Links
How To
How to Use the 5S to Increase Productivity In Manufacturing
5S stands for "Sort", 'Set In Order", 'Standardize', & Separate>. Toyota Motor Corporation developed the 5S method in 1954. It assists companies in improving their work environments and achieving higher efficiency.
This approach aims to standardize production procedures, making them predictable, repeatable, and easily measurable. This means that tasks such as cleaning, sorting, storing, packing, and labeling are performed daily. This knowledge allows workers to be more efficient in their work because they are aware of what to expect.
There are five steps that you need to follow in order to implement 5S. Each step is a different action that leads to greater efficiency. If you sort items, it makes them easier to find later. When items are ordered, they are put together. Then, after you separate your inventory into groups, you store those groups in containers that are easy to access. Finally, label all containers correctly.
Employees will need to be more critical about their work. Employees should understand why they do the tasks they do, and then decide if there are better ways to accomplish them. They must learn new skills and techniques in order to implement the 5S system.
The 5S method not only increases efficiency but also boosts morale and teamwork. As they begin to see improvements, they feel motivated to continue working towards the goal of achieving higher levels of efficiency.