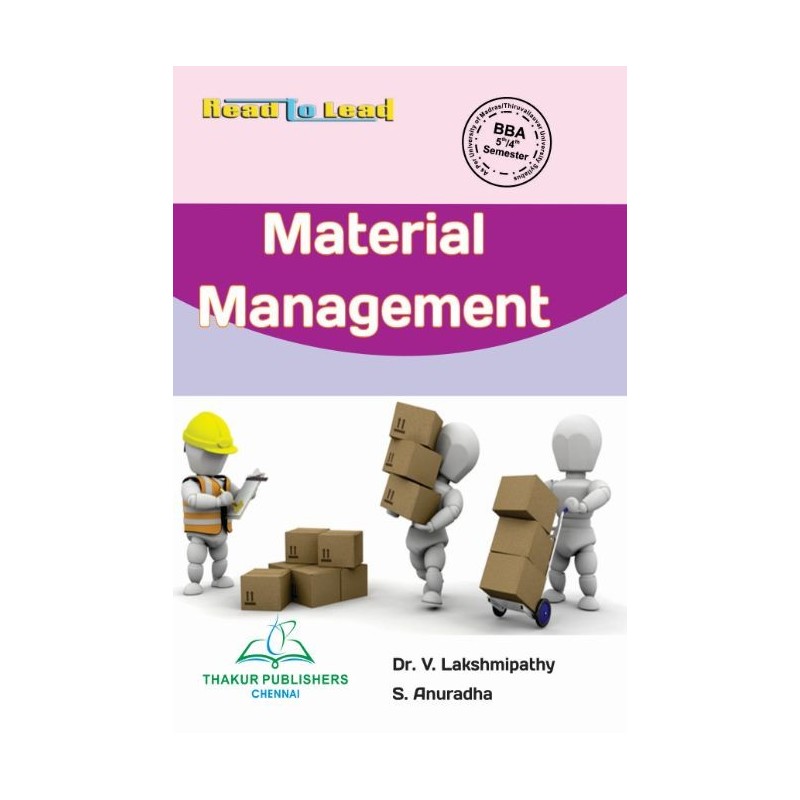
Industrial Engineering Jobs Houston
There are many industrial engineering positions in houston. These jobs offer a competitive pay, a challenging workplace and ample room to advance in your career.
Find entry-level industrial engineering jobs in Houston
Anyone who wants to start their career in the industry must apply for this entry-level position. This is a great opportunity to learn more about the company's values and people.
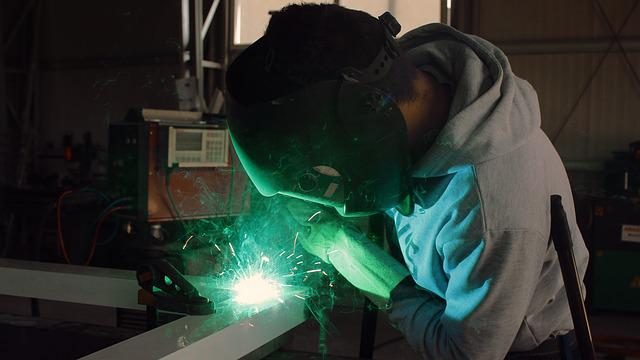
In addition to being an integral part of the company, this entry level position provides opportunities for you to improve your knowledge and skills through the above mentorship programs. This entry-level position also offers opportunities for professional development and many benefits, such as paid leave, health insurance plans, flexible spending account, tuition assistance programs, 401K plans with company matching, and an employee equity plan.
It is also a position at an entry level that pays just the right amount to get you from your cubicle into the workplace. This is a great opportunity to develop lasting relationships both with C&S and your colleagues.
The best part is that you'll be rewarded for your hard work with an awesome team. If this sounds like the right fit for you, apply today!
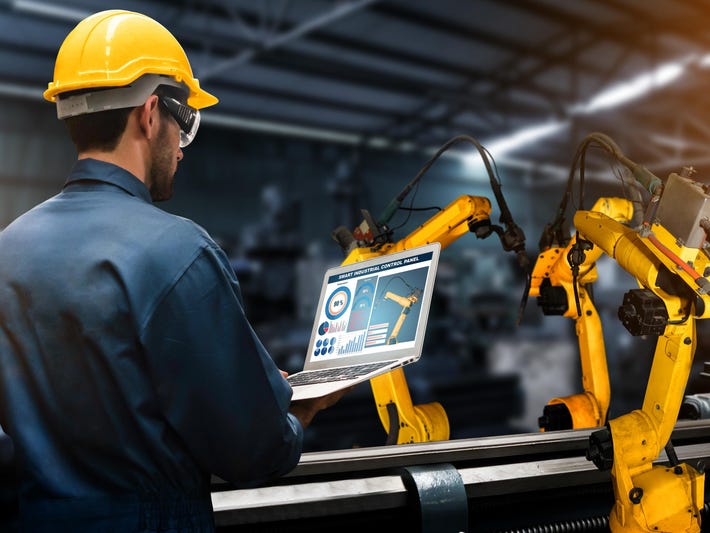
ARCXIS has been the leader in inspection, design and engineer services for residential building construction across more than 50 states.
FAQ
Is automation important for manufacturing?
Not only is automation important for manufacturers, but it's also vital for service providers. It allows them provide faster and more efficient services. It helps them to lower costs by reducing human errors, and improving productivity.
What are the responsibilities for a manufacturing manager
A manufacturing manager must make sure that all manufacturing processes run smoothly and effectively. They should also be aware of any problems within the company and act accordingly.
They should also be able and comfortable communicating with other departments like sales and marketing.
They must also keep up-to-date with the latest trends in their field and be able use this information to improve productivity and efficiency.
Can we automate some parts of manufacturing?
Yes! Yes. Automation has been around since ancient time. The Egyptians discovered the wheel thousands and years ago. To help us build assembly lines, we now have robots.
Robotics is used in many manufacturing processes today. These include:
-
Automation line robots
-
Robot welding
-
Robot painting
-
Robotics inspection
-
Robots that produce products
There are many other examples of how manufacturing could benefit from automation. For example, 3D printing allows us to make custom products without having to wait for weeks or months to get them manufactured.
What is meant by manufacturing industries?
Manufacturing Industries are companies that manufacture products. Consumers are people who purchase these goods. These companies employ many processes to achieve this purpose, such as production and distribution, retailing, management and so on. They manufacture goods from raw materials using machines and other equipment. This covers all types of manufactured goods including clothing, food, building supplies and furniture, as well as electronics, tools, machinery, vehicles and pharmaceuticals.
What are the 7 Rs of logistics management?
The acronym 7Rs of Logistics refers to the seven core principles of logistics management. It was published in 2004 by the International Association of Business Logisticians as part of their "Seven Principles of Logistics Management" series.
The acronym consists of the following letters:
-
Responsive - ensure all actions are legal and not harmful to others.
-
Reliable - Have confidence in your ability to fulfill all of your commitments.
-
Be responsible - Use resources efficiently and avoid wasting them.
-
Realistic - Take into consideration all aspects of operations including cost-effectiveness, environmental impact, and other factors.
-
Respectful: Treat others with fairness and equity
-
Be resourceful: Look for opportunities to save money or increase productivity.
-
Recognizable provides value-added products and services to customers
What is production planning?
Production planning is the process of creating a plan that covers all aspects of production. This includes scheduling, budgeting and crew, location, equipment, props, and more. This document is designed to make sure everything is ready for when you're ready to shoot. It should also contain information on achieving the best results on set. This includes information on shooting times, locations, cast lists and crew details.
It is important to first outline the type of film you would like to make. You may have already chosen the location you want, or there are locations or sets you prefer. Once you have identified your locations and scenes, you can start working out which elements you require for each scene. You might decide you need a car, but not sure what make or model. In this case, you could start looking up cars online to find out what models are available and then narrow your choices by choosing between different makes and models.
Once you have found the right car, you can start thinking about extras. Are you looking for people to sit in the front seats? Or perhaps you need someone walking around the back of the car? Perhaps you would like to change the interior colour from black to white. These questions will help to determine the style and feel of your car. You can also think about the type of shots you want to get. Will you be filming close-ups or wide angles? Maybe the engine or steering wheel is what you are looking to film. These factors will help you determine which car style you want to film.
Once you have determined all of the above, you can move on to creating a schedule. You can use a schedule to determine when and where you need it to be shot. A schedule for each day will detail when you should arrive at the location and when you need leave. So everyone is clear about what they need to do. It is possible to make arrangements in advance for additional staff if you are looking to hire. There is no point in hiring someone who won't turn up because you didn't let him know.
It is important to calculate the amount of filming days when you are creating your schedule. Some projects only take one or two days, while others may last weeks. When you are creating your schedule, you should always keep in mind whether you need more than one shot per day or not. Multiplying takes in the same area will result both in increased costs and a longer time. It is better to be cautious and take fewer shots than you risk losing money if you are not sure if multiple takes are necessary.
Budget setting is another important aspect in production planning. You will be able to manage your resources if you have a realistic budget. Remember that you can always reduce the budget later on if you run into unforeseen problems. However, you shouldn't overestimate the amount of money you will spend. You'll end up with less money after paying for other things if the cost is underestimated.
Production planning can be a complex process. However, once you know how everything works together it will become easier to plan future projects.
What is the job of a production plan?
A production planner makes sure all project elements are delivered on schedule, within budget, as well as within the agreed scope. A production planner ensures that the service and product meet the client's expectations.
Statistics
- You can multiply the result by 100 to get the total percent of monthly overhead. (investopedia.com)
- (2:04) MTO is a production technique wherein products are customized according to customer specifications, and production only starts after an order is received. (oracle.com)
- It's estimated that 10.8% of the U.S. GDP in 2020 was contributed to manufacturing. (investopedia.com)
- According to a Statista study, U.S. businesses spent $1.63 trillion on logistics in 2019, moving goods from origin to end user through various supply chain network segments. (netsuite.com)
- [54][55] These are the top 50 countries by the total value of manufacturing output in US dollars for its noted year according to World Bank.[56] (en.wikipedia.org)
External Links
How To
How to Use the Just In Time Method in Production
Just-intime (JIT), a method used to lower costs and improve efficiency in business processes, is called just-in-time. It is a process where you get the right amount of resources at the right moment when they are needed. This means that you only pay the amount you actually use. Frederick Taylor was the first to coin this term. He developed it while working as a foreman during the early 1900s. He noticed that workers were often paid overtime when they had to work late. He decided to ensure workers have enough time to do their jobs before starting work to improve productivity.
JIT teaches you to plan ahead and prepare everything so you don’t waste time. It is important to look at your entire project from beginning to end and ensure that you have enough resources to handle any issues that may arise. You will have the resources and people to solve any problems you anticipate. This will prevent you from spending extra money on unnecessary things.
There are many JIT methods.
-
Demand-driven: This JIT is where you place regular orders for the parts/materials that are needed for your project. This will allow to track how much material has been used up. It will also allow you to predict how long it takes to produce more.
-
Inventory-based : You can stock the materials you need in advance. This allows one to predict how much they will sell.
-
Project-driven: This is an approach where you set aside enough funds to cover the cost of your project. You will be able to purchase the right amount of materials if you know what you need.
-
Resource-based JIT: This is the most popular form of JIT. Here you can allocate certain resources based purely on demand. You might assign more people to help with orders if there are many. If you don't receive many orders, then you'll assign fewer employees to handle the load.
-
Cost-based: This is similar to resource-based, except that here you're not just concerned about how many people you have but how much each person costs.
-
Price-based: This is similar to cost-based but instead of looking at individual workers' salaries, you look at the total company price.
-
Material-based: This is quite similar to cost-based, but instead of looking at the total cost of the company, you're concerned with how much raw materials you spend on average.
-
Time-based: This is another variation of resource-based JIT. Instead of focusing solely on the amount each employee costs, focus on how long it takes for the project to be completed.
-
Quality-based: This is yet another variation of resource-based JIT. Instead of worrying about the costs of each employee or how long it takes for something to be made, you should think about how quality your product is.
-
Value-based JIT: This is the latest form of JIT. You don't worry about whether the products work or if they meet customer expectations. Instead, you focus on the added value that you provide to your market.
-
Stock-based: This is an inventory-based method that focuses on the actual number of items being produced at any given time. This is used to increase production and minimize inventory.
-
Just-in-time (JIT) planning: This is a combination of JIT and supply chain management. This refers to the scheduling of the delivery of components as soon after they are ordered. It's important because it reduces lead times and increases throughput.