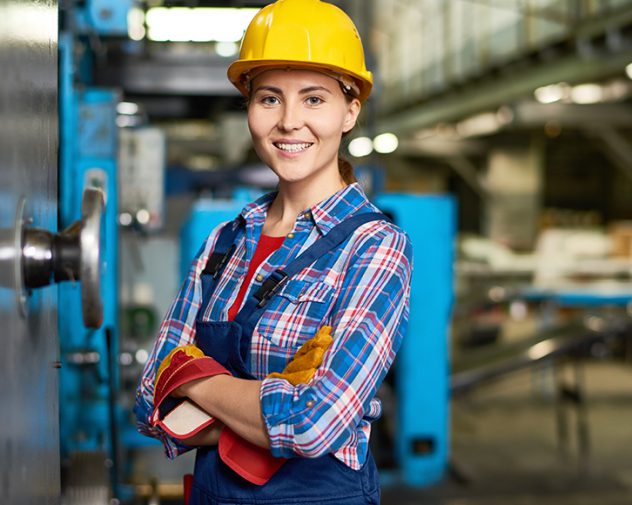
There are many types of manufacturing jobs. These jobs can include manufacturing, tool and die-making, assembly, fabrication, quality control, logistics, and operations. Advanced manufacturing can also be an option. This career offers higher challenges, greater pay and more success. This article will discuss the training paths for these jobs. Here are some common manufacturing jobs. Here are a few examples.
Manufacturing jobs include production, manufacturing, logistics, management, assembly, fabrication, tool and die-making, operations, quality control and processing.
There are many kinds of manufacturing careers. These jobs are becoming more technologically-oriented. They require advanced digital skills as well as comfort with technology. Job descriptions will require you to be organized, detail-oriented, and logical. While automation has not replaced human workers, it is changing the skills of workers. Manufacturing professionals are in high demand and their wages are generally higher than those of other professions. Many manufacturing workers are offered retirement benefits and health insurance.
Other careers in manufacturing involve fabricating and modifying apparel, tools, and machines, as well as maintaining industrial equipment and instruments. A lot of jobs in this field require knowledge and understanding of physical quantities, such as stress, strains, vibration frequency, pressure, and so on. The machines and equipment that mechanical engineers use, as well as textile technicians and packaging technologists, require them to understand both the electrical and mechanical aspects of their work.
All workers in a manufacturing firm share the responsibility for quality control. However, quality control workers are usually focused on monitoring the process of production and making sure that every part meets the requirements of the company. They may also be responsible for overseeing quality control processes and providing feedback to employees. A manufacturing career in quality control could help you advance your career by gaining valuable experience and education.
Advanced manufacturing jobs provide more opportunities, better pay, and a chance to achieve success.
Life in advanced manufacturing is more challenging, offers better opportunities and more pay. This growing industry makes use of technology and innovation to advance its processes and produce better products. High-paying careers in manufacturing require a lifetime commitment to success. The rewards are worth the difficulties. These jobs are ideal for those who love to be creative and innovative. Women are the future of manufacturing.
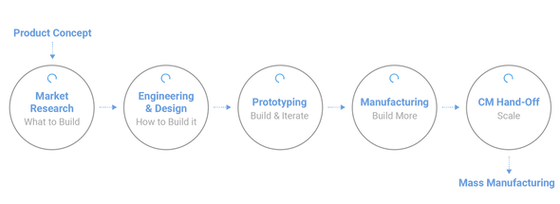
An advanced manufacturing position typically requires a college degree. An equivalent certificate can be obtained from post-secondary institutions. Manufacturing-focused higher-ed programs introduce students to cutting-edge manufacturing technologies and methodologies. These programs may include supply chain logistics and green manufacturing. These programs offer graduates in-demand skill development. The advantages of advanced manufacturing jobs include a higher salary, better benefits, and lifelong satisfaction.
The salary of an Advanced Manufacturing Engineer tends to be higher than that for a design engineer. This is because Advanced Manufacturing Engineers are typically more focused on design than on process capability. Advanced Manufacturing Engineers may have more solidworks and layout skills than others, but they are more popular in the Technology field. They can also find satisfaction in their work by meeting deadlines and making a positive difference in others' lives.
To get a job manufacturing, you need to learn how to train.
To pursue a career within manufacturing, there are many training options available. The manufacturing sector offers many rewarding career options and is in high demand. Although manufacturing was once associated with unskilled workers and dark factories, modern manufacturing is an industry that has many exciting career opportunities. Careers in this field are lean, green, high-tech, and highly creative.

A certificate in electrical engineering is necessary to be able to work as an assembler. You can further your skills by becoming a machinist or welding specialist, or as a quality controller specialist. You can even go on to become a plant manager, as the manufacturing industry requires many different types of workers. As a way of increasing your earning potential, you can pursue a career in manufacturing.
An entry-level position in a factory is another way to get a manufacturing training. Hudson Valley Community College partnered with several factories to offer their Entry Level program to people who are seeking entry-level jobs. This project was partially funded by Workforce Development Institute of New York. The program includes both online and hands-on classes. This program is perfect for individuals who don't have a lot of time for a full certificate or degree program.
FAQ
What are the 7 Rs of logistics management?
The acronym 7Rs of Logistics refers to the seven core principles of logistics management. It was created by the International Association of Business Logisticians and published in 2004 under its "Seven Principles of Logistics Management".
The acronym is composed of the following letters.
-
Responsive - ensure all actions are legal and not harmful to others.
-
Reliable - You can have confidence that you will fulfill your promises.
-
Be responsible - Use resources efficiently and avoid wasting them.
-
Realistic - Consider all aspects of operations, including environmental impact and cost effectiveness.
-
Respectful - treat people fairly and equitably.
-
Be resourceful: Look for opportunities to save money or increase productivity.
-
Recognizable - provide customers with value-added services.
How can we reduce manufacturing overproduction?
It is essential to find better ways to manage inventory to reduce overproduction. This would reduce time spent on activities such as purchasing, stocking, and maintaining excess stock. This would allow us to use our resources for more productive tasks.
A Kanban system is one way to achieve this. A Kanban Board is a visual display that tracks work progress. Work items are moved through various states to reach their destination in a Kanban system. Each state has a different priority level.
For instance, when work moves from one stage to another, the current task is complete enough to be moved to the next stage. However, if a task is still at the beginning stages, it will remain so until it reaches the end of the process.
This keeps work moving and ensures no work is lost. Managers can view the Kanban board to see how much work they have done. This allows them to adjust their workflows based on real-time information.
Lean manufacturing can also be used to reduce inventory levels. Lean manufacturing seeks to eliminate waste from every step of the production cycle. Anything that does not contribute to the product's value is considered waste. Some common types of waste include:
-
Overproduction
-
Inventory
-
Packaging not required
-
Material surplus
Manufacturers can reduce their costs and improve their efficiency by using these ideas.
What do you mean by warehouse?
A warehouse or storage facility is where goods are stored before they are sold. You can have it indoors or outdoors. In some cases it could be both indoors and outdoors.
What is the role and responsibility of a Production Planner?
Production planners ensure that all project aspects are completed on time, within budget and within the scope. They also ensure the quality of the product and service meets the client's requirements.
What does manufacturing industry mean?
Manufacturing Industries is a group of businesses that produce goods for sale. Consumers are those who purchase these products. This is accomplished by using a variety of processes, including production, distribution and retailing. They produce goods from raw materials by using machines and other machinery. This includes all types and varieties of manufactured goods, such as food items, clothings, building supplies, furnitures, toys, electronics tools, machinery vehicles, pharmaceuticals medical devices, chemicals, among others.
What are the four types in manufacturing?
Manufacturing refers the process of turning raw materials into useful products with machines and processes. It includes many different activities like designing, building and testing, packaging, shipping and selling, as well as servicing.
Statistics
- [54][55] These are the top 50 countries by the total value of manufacturing output in US dollars for its noted year according to World Bank.[56] (en.wikipedia.org)
- In 2021, an estimated 12.1 million Americans work in the manufacturing sector.6 (investopedia.com)
- According to the United Nations Industrial Development Organization (UNIDO), China is the top manufacturer worldwide by 2019 output, producing 28.7% of the total global manufacturing output, followed by the United States, Japan, Germany, and India.[52][53] (en.wikipedia.org)
- Many factories witnessed a 30% increase in output due to the shift to electric motors. (en.wikipedia.org)
- It's estimated that 10.8% of the U.S. GDP in 2020 was contributed to manufacturing. (investopedia.com)
External Links
How To
How to Use Six Sigma in Manufacturing
Six Sigma refers to "the application and control of statistical processes (SPC) techniques in order to achieve continuous improvement." Motorola's Quality Improvement Department created Six Sigma at their Tokyo plant, Japan in 1986. Six Sigma is a method to improve quality through standardization and elimination of defects. Many companies have adopted Six Sigma in recent years because they believe that there are no perfect products and services. Six Sigma seeks to reduce variation between the mean production value. This means that you can take a sample from your product and then compare its performance to the average to find out how often the process differs from the norm. If the deviation is excessive, it's likely that something needs to be fixed.
Understanding how variability works in your company is the first step to Six Sigma. Once you've understood that, you'll want to identify sources of variation. These variations can also be classified as random or systematic. Random variations occur when people make mistakes; systematic ones are caused by factors outside the process itself. Random variations would include, for example, the failure of some widgets to fall from the assembly line. You might notice that your widgets always fall apart at the same place every time you put them together.
Once you've identified where the problems lie, you'll want to design solutions to eliminate those problems. The solution could involve changing how you do things, or redesigning your entire process. Once you have implemented the changes, it is important to test them again to ensure they work. If they don't work you need to rework them and come up a better plan.