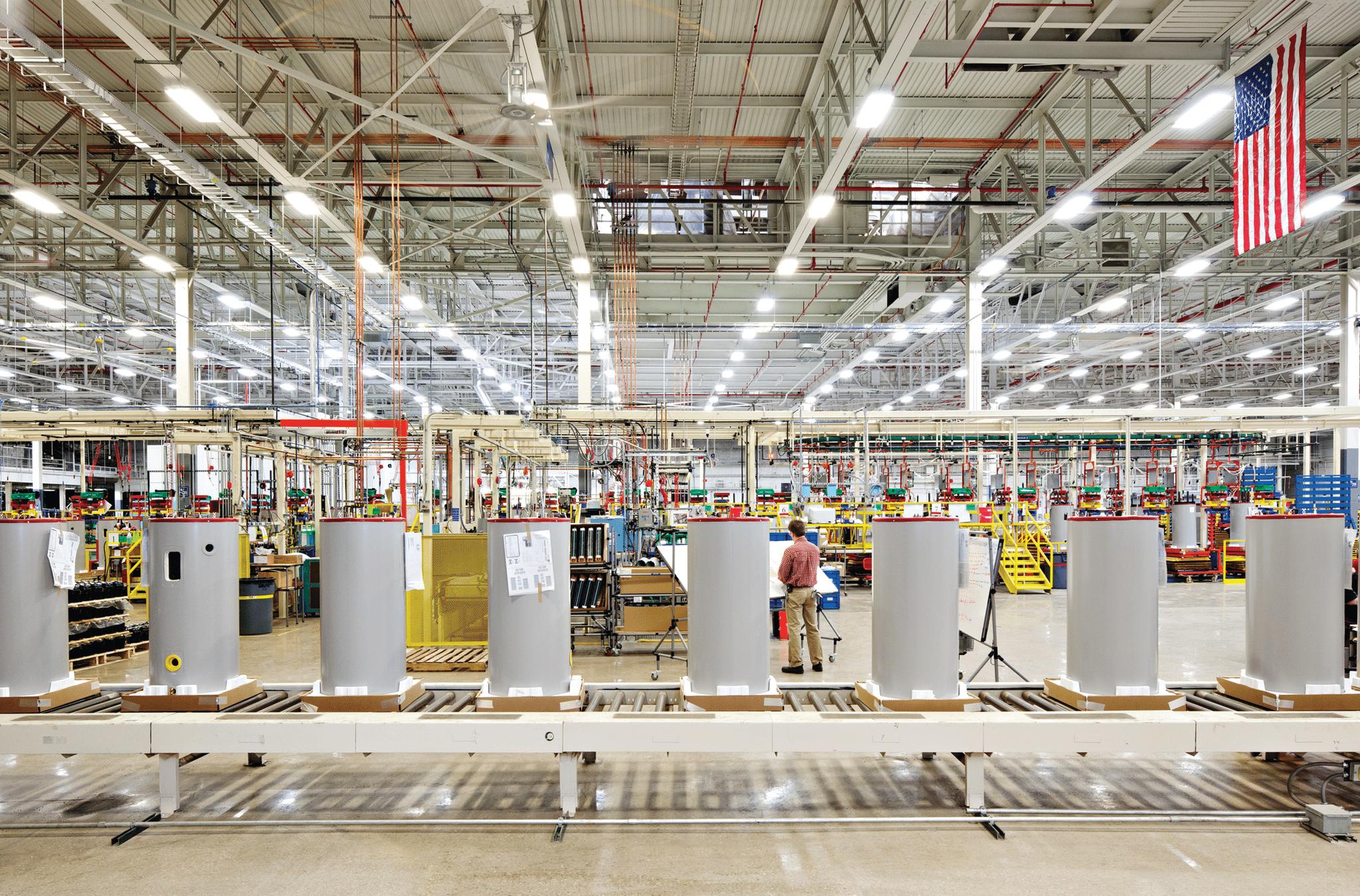
A single-piece flow production line can help increase your output and reduce inventory. It also helps to reduce lead times and lead times. Before you implement this technology, there are some things to be aware of. The takt time is the time taken to make an item. This allows you to calculate how quickly you need to produce an item to meet the demand of your customers.
One piece flow works best for low-variability products. But it isn't the right fit for every company. You want to make sure that you are measuring the right metrics to see if this type of process is right for your company.
The use of a single-piece flow will require a more robust, scalable control mechanism. This will help reduce waste and maximize efficiency. You should also ensure that the time needed to produce a single-piece item is sufficient to meet the requirements of your customers. This will ensure that one-piece production doesn't suffer from the same efficiency as traditional production.
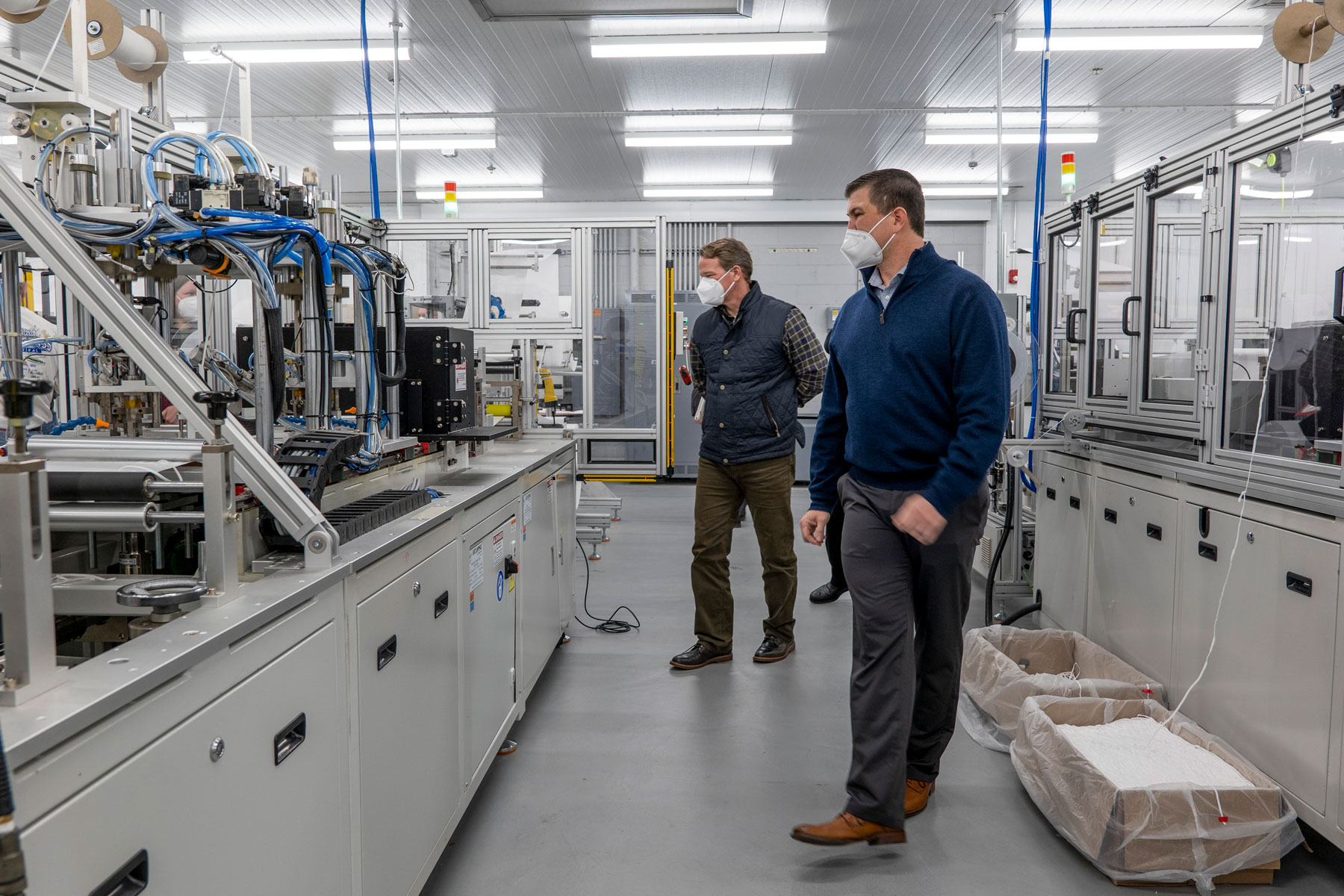
One piece flow is achieved by using a production process that looks like an U or S. This is because it will reduce the amount of movement required to move from step to step. It also allows for greater assembly efficiency.
The lean process also has an associated term, the poka-yoke, which is a clever way to prevent defects from moving to the next step. This is a great way to save time and money while increasing the quality of your products. Poka-yoke can also reduce waste and inefficiency.
If there is a high demand of individual products, one-piece flow works well. This is when you don't want to waste time or money by mixing different items together from one order. A single flow for a work item will reduce delays and decrease inventory depreciation. It will also reduce the time products spend in the warehouse (WIP).
For a lower cost, you could also use a single part flow process to maintain your inventory. This is especially important to small businesses. This process will allow you to save money on inventory storage, transportation, and repackaging of your products. This process is also a great option to shorten the time it takes for customers to receive your products.
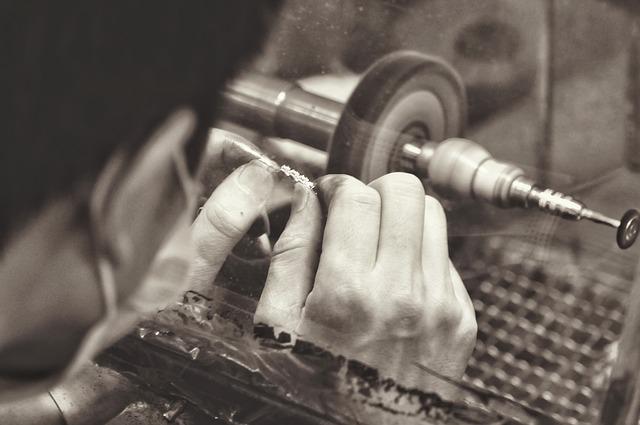
Employee morale is also improved by the one-piece flow process. It allows employees to work together. It is also easier to identify potential problems with your product. This is crucial because customers could be sent items that are not complete or defective. This is another great way to improve your customer care.
The one-piece flow production line is versatile and can be used both inside an assembly line and outside. This process allows you to maximize your value stream. This type of process also allows for faster production and high quality products. It can be used to increase employee morale and reduce costs.
FAQ
What makes a production planner different from a project manger?
The main difference between a production planner and a project manager is that a project manager is usually the person who plans and organizes the entire project, whereas a production planner is mainly involved in the planning stage of the project.
What are manufacturing and logistic?
Manufacturing is the act of producing goods from raw materials using machines and processes. Logistics is the management of all aspects of supply chain activities, including procurement, production planning, distribution, warehousing, inventory control, transportation, and customer service. Manufacturing and logistics are often considered together as a broader term that encompasses both the process of creating products and delivering them to customers.
What does manufacturing mean?
Manufacturing Industries are those businesses that make products for sale. Consumers are people who purchase these goods. These companies employ many processes to achieve this purpose, such as production and distribution, retailing, management and so on. They manufacture goods from raw materials using machines and other equipment. This includes all types and varieties of manufactured goods, such as food items, clothings, building supplies, furnitures, toys, electronics tools, machinery vehicles, pharmaceuticals medical devices, chemicals, among others.
Statistics
- It's estimated that 10.8% of the U.S. GDP in 2020 was contributed to manufacturing. (investopedia.com)
- [54][55] These are the top 50 countries by the total value of manufacturing output in US dollars for its noted year according to World Bank.[56] (en.wikipedia.org)
- According to a Statista study, U.S. businesses spent $1.63 trillion on logistics in 2019, moving goods from origin to end user through various supply chain network segments. (netsuite.com)
- Many factories witnessed a 30% increase in output due to the shift to electric motors. (en.wikipedia.org)
- According to the United Nations Industrial Development Organization (UNIDO), China is the top manufacturer worldwide by 2019 output, producing 28.7% of the total global manufacturing output, followed by the United States, Japan, Germany, and India.[52][53] (en.wikipedia.org)
External Links
How To
How to use the Just-In Time Method in Production
Just-intime (JIT), a method used to lower costs and improve efficiency in business processes, is called just-in-time. It is a process where you get the right amount of resources at the right moment when they are needed. This means you only pay what you use. The term was first coined by Frederick Taylor, who developed his theory while working as a foreman in the early 1900s. He observed how workers were paid overtime if there were delays in their work. He decided that workers would be more productive if they had enough time to complete their work before they started to work.
JIT is a way to plan ahead and make sure you don't waste any money. You should also look at the entire project from start to finish and make sure that you have sufficient resources available to deal with any problems that arise during the course of your project. If you anticipate that there might be problems, you'll have enough people and equipment to fix them. This way you won't be spending more on things that aren’t really needed.
There are different types of JIT methods:
-
Demand-driven: This JIT is where you place regular orders for the parts/materials that are needed for your project. This will allow to track how much material has been used up. It will also allow you to predict how long it takes to produce more.
-
Inventory-based: This allows you to store the materials necessary for your projects in advance. This allows for you to anticipate how much you can sell.
-
Project-driven: This means that you have enough money to pay for your project. When you know how much you need, you'll purchase the appropriate amount of materials.
-
Resource-based JIT: This type of JIT is most commonly used. This is where you assign resources based upon demand. For example, if there is a lot of work coming in, you will have more people assigned to them. If you don't receive many orders, then you'll assign fewer employees to handle the load.
-
Cost-based: This is a similar approach to resource-based but you are not only concerned with how many people you have, but also how much each one costs.
-
Price-based: This is a variant of cost-based. However, instead of focusing on the individual workers' costs, this looks at the total price of the company.
-
Material-based - This is a variant of cost-based. But instead of looking at the total company cost, you focus on how much raw material you spend per year.
-
Time-based JIT: This is another variant of resource-based JIT. Instead of focusing on the cost of each employee, you will focus on the time it takes to complete a project.
-
Quality-based: This is yet another variation of resource-based JIT. Instead of focusing on the cost of each worker or how long it takes, think about how high quality your product is.
-
Value-based JIT: One of the most recent forms of JIT. In this scenario, you're not concerned about how products perform or whether customers expect them to meet their expectations. Instead, you focus on the added value that you provide to your market.
-
Stock-based is an inventory-based system that measures the number of items produced at any given moment. This method is useful when you want to increase production while decreasing inventory.
-
Just-in time (JIT), planning: This is a combination JIT/supply chain management. It's the process of scheduling delivery of components immediately after they are ordered. This is important as it reduces lead time and increases throughput.