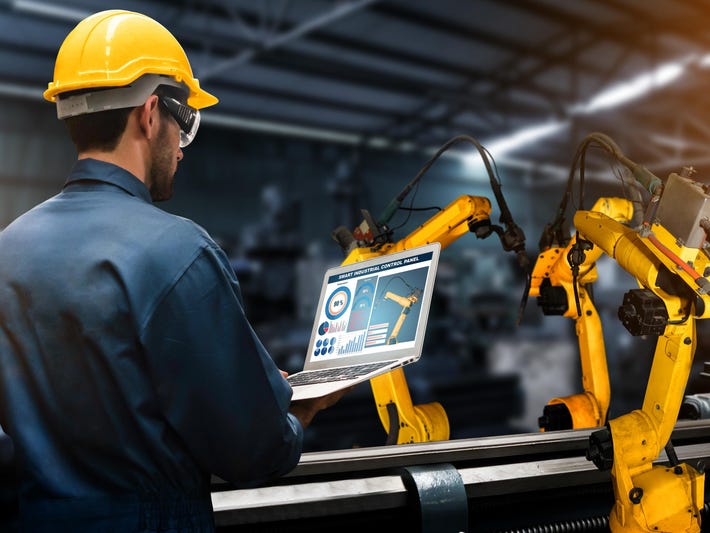
Supply chain management software will help you improve your efficiency and streamline your processes, no matter if you work for a large corporation or small business. These systems offer a centralized view of your entire supply chain, allowing you to plan production, shipment planning, and delivery routes. These systems allow you to automate and streamline your processes, allowing your employees to concentrate on other aspects of the business. Software for supply chain management is essential to any organization that handles shipping and manufacturing.
You need to consider many features and capabilities when selecting the best supply chain management tool. These include scalability as well as ease-of use and integration with other apps. You should also consider the provider's reputation and the features they offer. Additionally, it is important to find a solution within your budget. You can adjust to your business's needs, regardless of whether you go for a SaaS or full-scale solution.
E2open, one of the most trusted supply chain management software companies, specializes in cloud-based solution that improves demand forecasting and operations management. The company also offers advanced features and a technology platform. The software can be used by businesses in all industries, such as manufacturing, transport, and retail.
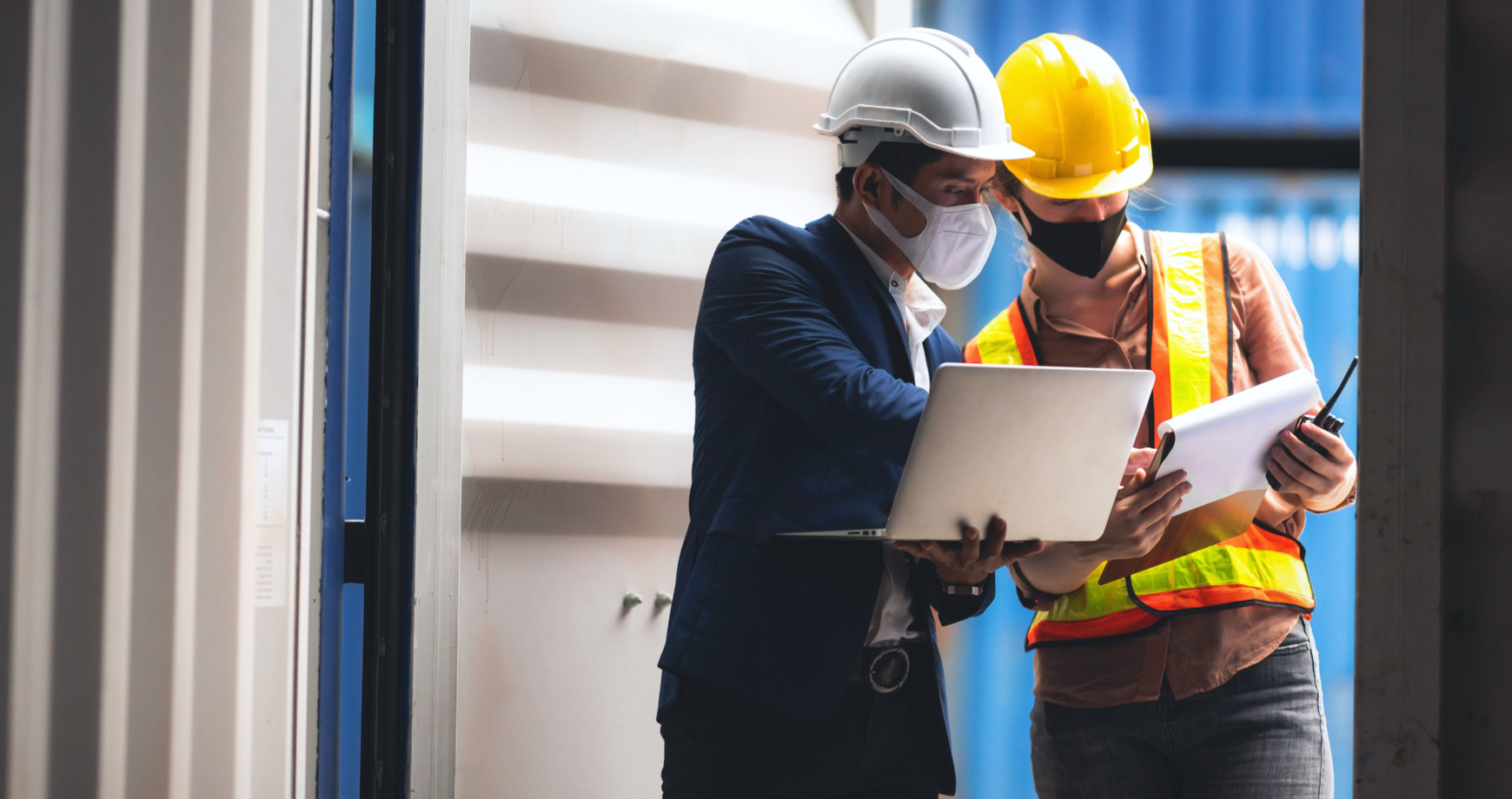
The key feature of supply-chain management software is real time visibility. This helps you monitor your inventory, as well as shipments, to keep track of your products. It ensures that customers receive what they require when they are needed. It can also help you devise long-term strategies to balance demand and supply.
Kinaxis is a comprehensive supply chain management software solution that breaks down silos and streamlines processes. It combines machine and human intelligence to help you make better business decisions. It can also be used to plan inventory and capacity in order to better respond for opportunities.
The sales forecasting software helps you better understand past sales, sales cycles and seasonality. It also makes use of machine learning to predict future sales. This software helps you predict your sales, and it also prepares your sales team for the future. This software also allows you to access data from many sources, making it easier to view the entire picture of your operation.
Descartes Systems Group, the biggest competitor to supply-chain management software, is their main competitor. They are the top vendor for many organizations. This company is home to over 13,000 active users. Its products are competitive with SAP SCM (SAP Megaventory), JDA, Logility, and JDA.
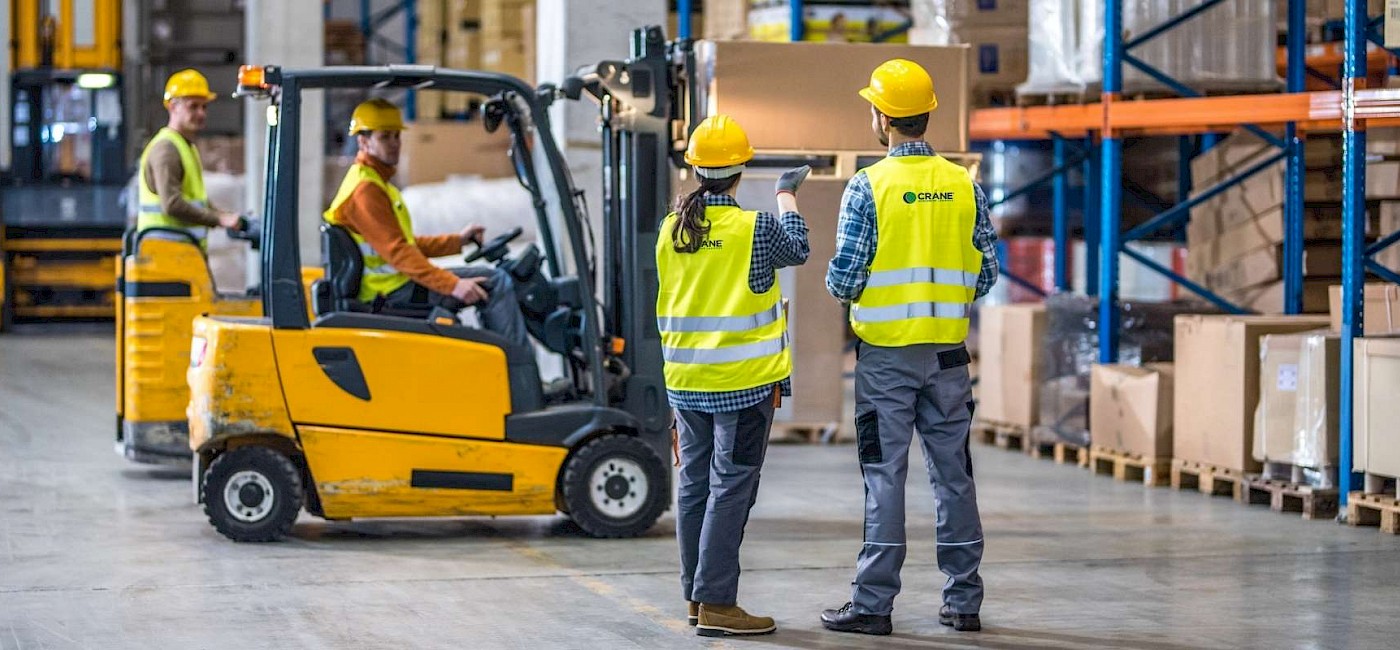
Manhattan Associates is another competitor to supply-chain management software. This software company boasts thousands of users and a revenue of approximately $617.5million. Eddie Capel runs the company. This company competes against JDA, Logility, and Infor SCM.
Infor SCM is one of the best supply chain management software platforms. It is a perfect solution for businesses of any size and one of the most widely-used supply chain management platforms. It is cloud-based and unites all aspects of enterprise operations. It also includes analytics at the core, which can help you optimize your end-to-end supply chain.
FAQ
What is the difference between Production Planning and Scheduling?
Production Planning (PP), also known as forecasting and identifying production capacities, is the process that determines what product needs to be produced at any particular time. Forecasting demand is one way to do this.
Scheduling refers to the process of allocating specific dates to tasks in order that they can be completed within a specified timeframe.
What is the responsibility of a production planner?
Production planners ensure that all project aspects are completed on time, within budget and within the scope. They make sure that the product and services meet client expectations.
What are the 7 R's of logistics?
The acronym "7R's" of Logistics stands for seven principles that underpin logistics management. It was developed by the International Association of Business Logisticians (IABL) and published in 2004 as part of its "Seven Principles of Logistics Management" series.
The acronym consists of the following letters:
-
Responsible - to ensure that all actions are within the legal requirements and are not detrimental to others.
-
Reliable - You can have confidence that you will fulfill your promises.
-
It is reasonable to use resources efficiently and not waste them.
-
Realistic - Take into consideration all aspects of operations including cost-effectiveness, environmental impact, and other factors.
-
Respectful: Treat others with fairness and equity
-
You are resourceful and look for ways to save money while increasing productivity.
-
Recognizable is a company that provides customers with value-added solutions.
What are the requirements to start a logistics business?
To run a successful logistics company, you need a lot knowledge and skills. Effective communication skills are necessary to work with suppliers and clients. You will need to know how to interpret data and draw conclusions. You will need to be able handle pressure well and work in stressful situations. To improve efficiency, you must be innovative and creative. Strong leadership qualities are essential to motivate your team and help them achieve their organizational goals.
It is important to be organized and efficient in order to meet tight deadlines.
How can manufacturing efficiency be improved?
First, identify the factors that affect production time. We then need to figure out how to improve these variables. You can start by identifying the most important factors that impact production time. Once you've identified them all, find solutions to each one.
What is the role of a logistics manager
Logistics managers are responsible for ensuring that all goods arrive in perfect condition and on time. This is achieved by using their knowledge and experience with the products of the company. He/she should ensure that sufficient stock is available in order to meet customer demand.
Can we automate some parts of manufacturing?
Yes! Since ancient times, automation has been in existence. The Egyptians created the wheel thousands years ago. Robots are now used to assist us in assembly lines.
In fact, there are several applications of robotics in manufacturing today. These include:
-
Robots for assembly line
-
Robot welding
-
Robot painting
-
Robotics inspection
-
Robots that produce products
Manufacturing can also be automated in many other ways. For example, 3D printing allows us to make custom products without having to wait for weeks or months to get them manufactured.
Statistics
- You can multiply the result by 100 to get the total percent of monthly overhead. (investopedia.com)
- Job #1 is delivering the ordered product according to specifications: color, size, brand, and quantity. (netsuite.com)
- [54][55] These are the top 50 countries by the total value of manufacturing output in US dollars for its noted year according to World Bank.[56] (en.wikipedia.org)
- It's estimated that 10.8% of the U.S. GDP in 2020 was contributed to manufacturing. (investopedia.com)
- In the United States, for example, manufacturing makes up 15% of the economic output. (twi-global.com)
External Links
How To
How to use 5S to increase Productivity in Manufacturing
5S stands to stand for "Sort", “Set In Order", “Standardize", and "Store". The 5S methodology was developed at Toyota Motor Corporation in 1954. It assists companies in improving their work environments and achieving higher efficiency.
This method aims to standardize production processes so that they are repeatable, measurable and predictable. It means tasks like cleaning, sorting or packing, labeling, and storing are done every day. This knowledge allows workers to be more efficient in their work because they are aware of what to expect.
Implementing 5S requires five steps. These are Sort, Set In Order, Standardize. Separate. And Store. Each step has a different action and leads to higher efficiency. For example, when you sort things, you make them easy to find later. Once you have placed items in an ordered fashion, you will put them together. Then, after you separate your inventory into groups, you store those groups in containers that are easy to access. Finally, label all containers correctly.
Employees will need to be more critical about their work. Employees must be able to see why they do what they do and find a way to achieve them without having to rely on their old methods. To be successful in the 5S system, employees will need to acquire new skills and techniques.
The 5S method not only increases efficiency but also boosts morale and teamwork. They feel more motivated to work towards achieving greater efficiency as they see the results.