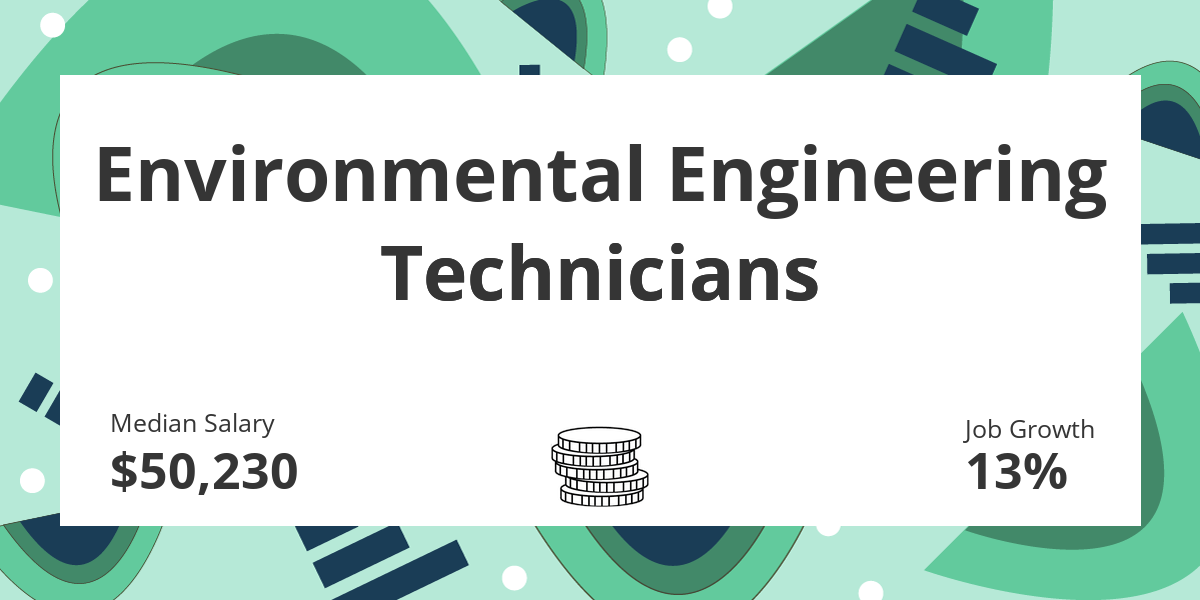
Interested in learning about the environmental engineers salary? Here's a quick overview on the average annual salary for environmental engineers. Read on for information about the career outlook and requirements to be one. We will be discussing the salary requirements and the future employment prospects for environmental engineers in this article. The average environmental engineers salary is $59,870 per year. However, you should know that you could earn much more. You will need a bachelor's degree or equivalent in environmental engineering to get started.
Average annual income
The average annual salary for environmental engineers is $96,820, and is expected to grow slightly faster than the average for all occupations. There are approximately 4,000 job openings each year. This is mainly due to the retirement of workers or their transition to other jobs. Check out the salaries of similar jobs to see if your experience or degree matches what is required for an environmental engineer.
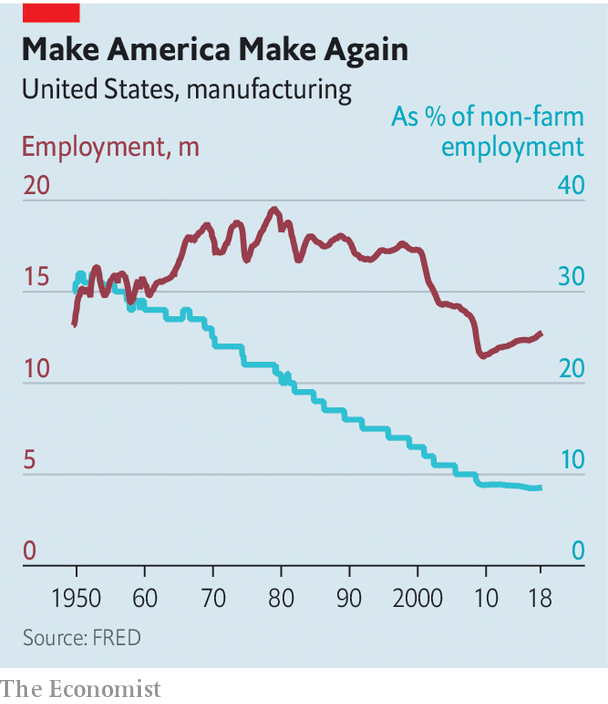
The average annual salary of an environmental engineer is not set, but this field provides both meaning and financial work. The BLS reported an average annual wage of $101,640 for federal government environmental engineers, with the top 10 percent earning more than $128,000. There are however variations within the profession, with the highest-paid earning individuals making more than $150,000 while the lowest-paid workers earning less that $67,000.
Environmental engineers have a bright future.
According to the Bureau of Labor Statistics, the employment outlook for environmental engineers is positive. There will be an increase of 3.23% in the number of environmental engineer jobs from 2004 to 2024. It is slightly lower than what the national average is. There will be another 7,350 job openings in the near future. This is an increase of 1.63 percent per year. The growth in job opportunities is expected to be modest.
As the world becomes more conscious about the effects of human beings on the environment, the demand for environmental engineers will increase. This is due in part to a greater awareness of the environmental effects and the need to find solutions. This makes it easy for environmental engineers to get hired. According to the U.S. Bureau of Labor Statistics (USBLS), environmental engineers will see a 12 percent increase in demand between 2014 and 2024. It's a good idea to earn a degree or certificate in environmental engineering.
What are the requirements to become an environmental engineer?
After earning a bachelor's degree in engineering, environmental engineers are eligible to take the FE (Foundational Examination), a test that tests their basic knowledge and understanding of the environment. These engineers are sometimes called "engineer interns" and/or "engineer-in-training" until they can take Principles and Practice of Engineering exams (PPE). While many states require the continued education of environmental engineers, most will recognize prior licensure. Additionally, environmental engineers can earn board certification from the American Academy of Environmental Engineers (AACE), a mark of experience that demonstrates the level of expertise they have in a particular area of environmental engineering.
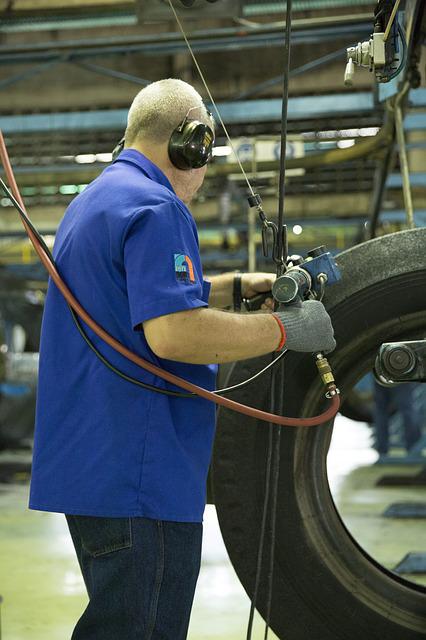
There are many other skills that are required in order to be an environmental engineer, beyond a bachelor's degree. Environment engineers need to be imaginative and able think about how their designs or solutions will impact larger systems. They must communicate well with others and be able work independently. They need to be able work with scientists and engineers of other specialties. They should also be able write clearly.
FAQ
Why is logistics important for manufacturing?
Logistics are essential to any business. Logistics can help you achieve amazing results by helping to manage product flow from raw materials to finished products.
Logistics also play a major role in reducing costs and increasing efficiency.
What type of jobs is there in logistics
There are many jobs available in logistics. Here are some examples:
-
Warehouse workers - They load trucks and pallets.
-
Transport drivers - These are people who drive trucks and trailers to transport goods or perform pick-ups.
-
Freight handlers – They sort and package freight at warehouses.
-
Inventory managers - These are responsible for overseeing the stock of goods in warehouses.
-
Sales representatives: They sell products to customers.
-
Logistics coordinators – They plan and coordinate logistics operations.
-
Purchasing agents - They purchase goods and services needed for company operations.
-
Customer service representatives - Answer calls and email from customers.
-
Shippers clerks - They process shipping order and issue bills.
-
Order fillers are people who fill orders based only on what was ordered.
-
Quality control inspectors (QCI) - They inspect all incoming and departing products for potential defects.
-
Others - There is a variety of other jobs in logistics. These include transportation supervisors and cargo specialists.
Can we automate some parts of manufacturing?
Yes! Automation has been around since ancient times. The wheel was invented by the Egyptians thousands of years ago. Robots are now used to assist us in assembly lines.
Robotics is used in many manufacturing processes today. These include:
-
Assembly line robots
-
Robot welding
-
Robot painting
-
Robotics inspection
-
Robots that make products
Manufacturing could also benefit from automation in other ways. 3D printing makes it possible to produce custom products in a matter of days or weeks.
Is automation important in manufacturing?
Not only are service providers and manufacturers important, but so is automation. It allows them to offer services faster and more efficiently. It helps them to lower costs by reducing human errors, and improving productivity.
Statistics
- According to the United Nations Industrial Development Organization (UNIDO), China is the top manufacturer worldwide by 2019 output, producing 28.7% of the total global manufacturing output, followed by the United States, Japan, Germany, and India.[52][53] (en.wikipedia.org)
- You can multiply the result by 100 to get the total percent of monthly overhead. (investopedia.com)
- Job #1 is delivering the ordered product according to specifications: color, size, brand, and quantity. (netsuite.com)
- (2:04) MTO is a production technique wherein products are customized according to customer specifications, and production only starts after an order is received. (oracle.com)
- In 2021, an estimated 12.1 million Americans work in the manufacturing sector.6 (investopedia.com)
External Links
How To
How to use the Just In-Time Production Method
Just-in time (JIT), is a process that reduces costs and increases efficiency in business operations. It is a process where you get the right amount of resources at the right moment when they are needed. This means that only what you use is charged to your account. Frederick Taylor first coined this term while working in the early 1900s as a foreman. Taylor observed that overtime was paid to workers if they were late in working. He decided to ensure workers have enough time to do their jobs before starting work to improve productivity.
JIT is about planning ahead. You should have all the necessary resources ready to go so that you don’t waste money. You should also look at the entire project from start to finish and make sure that you have sufficient resources available to deal with any problems that arise during the course of your project. You can anticipate problems and have enough equipment and people available to fix them. You won't have to pay more for unnecessary items.
There are several types of JIT techniques:
-
Demand-driven: This is a type of JIT where you order the parts/materials needed for your project regularly. This will allow you to track how much material you have left over after using it. This will allow to you estimate the time it will take for more to be produced.
-
Inventory-based: This is a type where you stock the materials required for your projects in advance. This allows for you to anticipate how much you can sell.
-
Project-driven: This approach involves setting aside sufficient funds to cover your project's costs. Knowing how much money you have available will help you purchase the correct amount of materials.
-
Resource-based JIT: This type of JIT is most commonly used. Here you can allocate certain resources based purely on demand. You might assign more people to help with orders if there are many. If there aren't many orders, you will assign fewer people.
-
Cost-based : This is similar in concept to resource-based. But here, you aren't concerned about how many people your company has but how much each individual costs.
-
Price-based pricing: This is similar in concept to cost-based but instead you look at how much each worker costs, it looks at the overall company's price.
-
Material-based: This is quite similar to cost-based, but instead of looking at the total cost of the company, you're concerned with how much raw materials you spend on average.
-
Time-based: Another variation of resource-based JIT. Instead of focusing on how much each employee costs, you focus on how long it takes to complete the project.
-
Quality-based JIT is another variant of resource-based JIT. Instead of focusing on the cost of each worker or how long it takes, think about how high quality your product is.
-
Value-based JIT is the newest form of JIT. This is where you don't care about how the products perform or whether they meet customers' expectations. Instead, you are focused on adding value to the marketplace.
-
Stock-based is an inventory-based system that measures the number of items produced at any given moment. It's used when you want to maximize production while minimizing inventory.
-
Just-in time (JIT), planning: This is a combination JIT/supply chain management. It is the process that schedules the delivery of components within a short time of their order. This is important as it reduces lead time and increases throughput.