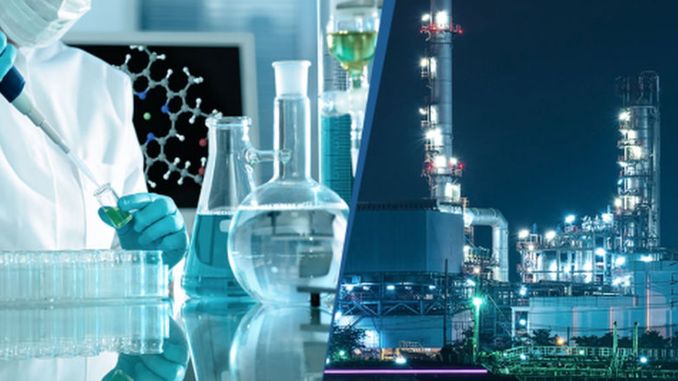
Typically, tool and die makers work in machine shops. They are responsible for operating lathes, milling machines, as well as other types of machine tools. They also repair tools and make dies for machine machinists. They might also design tools for customers.
Tool and die makers are required to maintain high standards of quality and precision in their work. They verify the accuracy of their work, and inspect finished products. Tool and die makers may work with engineers to improve processes. Sometimes they will travel to the customer's place to inspect how the tool works. They are also expected to keep their work area clean and organized. They may wear protective gear. They may suggest additional tools to improve efficiency.
The typical work week for tool and die makers is 40 hours. They might also be expected to do some moderately heavy lifting. They must also have strong academic backgrounds. Employers may prefer an associate's, bachelor's, or master's degree in a similar field. They might also receive training on-the-job or apprentice programs.
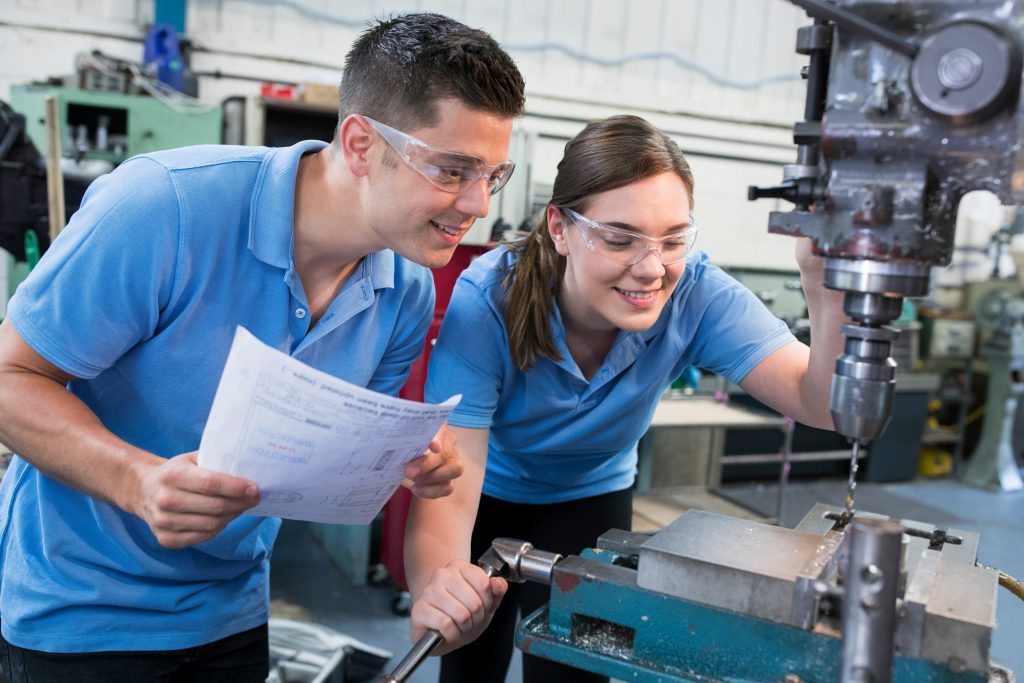
Four-year apprenticeship programs for tool and diemakers are typically offered by employers. They will receive on-thejob training from an expert worker during the apprenticeship program. They also participate in technical college classes at night. This program offers both classroom instruction and hands-on training. They may also have the opportunity to program computercontrolled machine tools. They may be eligible to move up to supervisory posts.
Tool and die makers typically have a high school diploma or equivalent. They might also hold a degree or certificate in a technical area, such as engineering or physics. They may also have some prior training in science or math. This training can often prove to be helpful.
Tool and diemakers need good eyesight. They need to be patient and able to focus. They need to have physical strength in order to work with machinery. They should also have a strong work ethic. They should be able and able to read technical drawings and specifications. They should also possess good interpersonal skills. They should also have strong computer skills. They may also be required to maintain computer numerically controlled (CNC) machines.
A tool and die maker must be analytical. They have to understand how tools and dies work and how to repair them. They also need to be problem-solving and have mechanical aptitude. They may also be required to learn new methods of machining. They will need to be proficient in digital skills like computer-aided planning (CAD) and computer aided manufacturing (CAM). They should also be skilled in sales. They should be able and willing to work both independently and collaboratively.
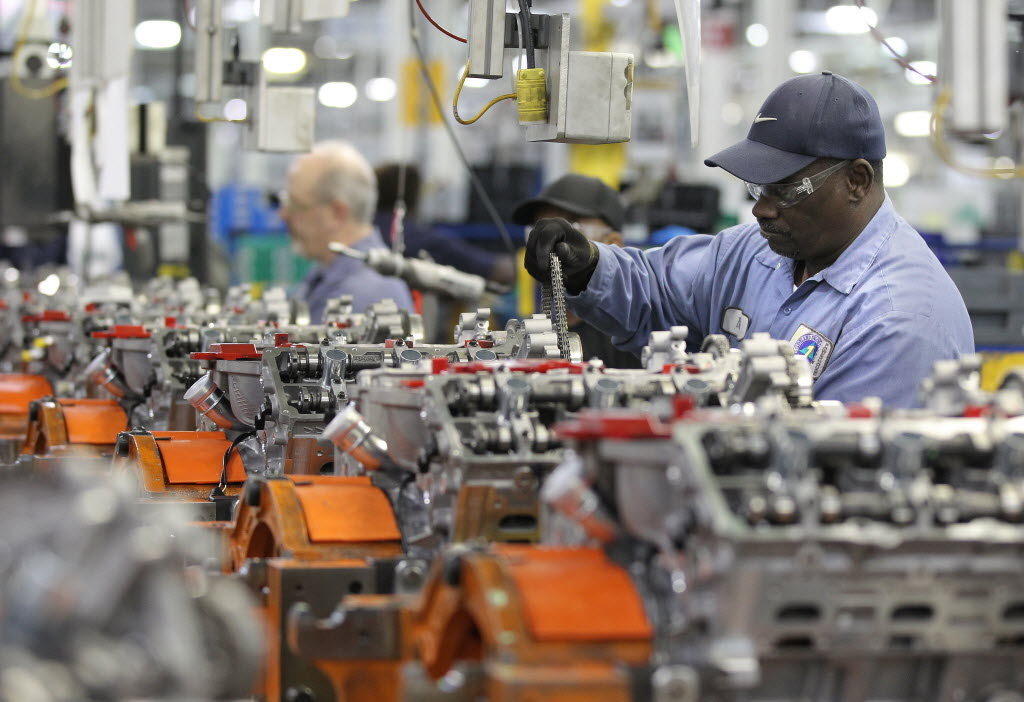
Apprentices can expect to work 40 hours per semaine during an apprenticeship program. Apprentices attend classes at night and then work during the day on a job. They take on more challenging tasks eventually. For most apprenticeships, you will need a high school diploma. They should also take courses on science and math.
Some tool- and die-makers continue their education by obtaining a bachelor's, master's, or doctoral degree. Average income for tool and denter makers is $56,186. But, they are likely to see a decrease in their job prospects due to automation.
FAQ
How important is automation in manufacturing?
Not only is automation important for manufacturers, but it's also vital for service providers. Automation allows them to deliver services quicker and more efficiently. It also helps to reduce costs and improve productivity.
What are the logistics products?
Logistics refers to the movement of goods from one place to another.
They cover all aspects of transportation, such as packing, loading, transporting and unloading.
Logisticians ensure the product reaches its destination in the most efficient manner. They help companies manage their supply chain efficiency by providing information on demand forecasts, stock levels, production schedules, and availability of raw materials.
They monitor shipments in transit, ensure quality standards, manage inventories, replenish orders, coordinate with suppliers and other vendors, and offer support services for sales, marketing, and customer service.
What are manufacturing and logistic?
Manufacturing refers the process of producing goods from raw materials through machines and processes. Logistics manages all aspects of the supply chain, including procurement, production planning and distribution, inventory control, transportation, customer service, and transport. Manufacturing and logistics can often be grouped together to describe a larger term that covers both the creation of products, and the delivery of them to customers.
Statistics
- You can multiply the result by 100 to get the total percent of monthly overhead. (investopedia.com)
- According to the United Nations Industrial Development Organization (UNIDO), China is the top manufacturer worldwide by 2019 output, producing 28.7% of the total global manufacturing output, followed by the United States, Japan, Germany, and India.[52][53] (en.wikipedia.org)
- It's estimated that 10.8% of the U.S. GDP in 2020 was contributed to manufacturing. (investopedia.com)
- (2:04) MTO is a production technique wherein products are customized according to customer specifications, and production only starts after an order is received. (oracle.com)
- Job #1 is delivering the ordered product according to specifications: color, size, brand, and quantity. (netsuite.com)
External Links
How To
How to use 5S to increase Productivity in Manufacturing
5S stands to stand for "Sort", “Set In Order", “Standardize", and "Store". Toyota Motor Corporation was the first to develop the 5S approach in 1954. This methodology helps companies improve their work environment to increase efficiency.
This method has the basic goal of standardizing production processes to make them repeatable. This means that daily tasks such as cleaning and sorting, storage, packing, labeling, and packaging are possible. This knowledge allows workers to be more efficient in their work because they are aware of what to expect.
Implementing 5S involves five steps: Sort, Set in Order, Standardize Separate, Store, and Each step requires a different action, which increases efficiency. You can make it easy for people to find things later by sorting them. Once you have placed items in an ordered fashion, you will put them together. Then, after you separate your inventory into groups, you store those groups in containers that are easy to access. Finally, when you label your containers, you ensure everything is labeled correctly.
This requires employees to critically evaluate how they work. Employees must be able to see why they do what they do and find a way to achieve them without having to rely on their old methods. To be successful in the 5S system, employees will need to acquire new skills and techniques.
In addition to increasing efficiency, the 5S method also improves morale and teamwork among employees. As they begin to see improvements, they feel motivated to continue working towards the goal of achieving higher levels of efficiency.