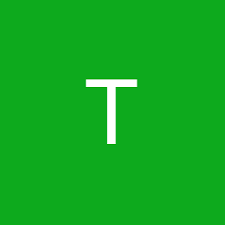
Typically, tool and die makers work in machine shops. They use lathes, milling machine, and other types to operate machines. They repair tools and dies that are used by machinists. They may also design tools for customers.
High standards of precision and quality are expected from tool and die manufacturers. They ensure that their work is accurate and inspect finished products. Tool and die makers may work with engineers to improve processes. Sometimes they will travel to the customer's place to inspect how the tool works. They are required to keep their work space clean and organized. They might wear protective gear. They may suggest additional tools to improve efficiency.
Tool and die-makers typically work 40 hours per week. They may also be expected to do moderately heavy lifting. They are also required to have a strong educational background. Employers often prefer applicants with an associate's (or bachelor's) degree in a related field. They may also receive on-the job training or apprentice programs.
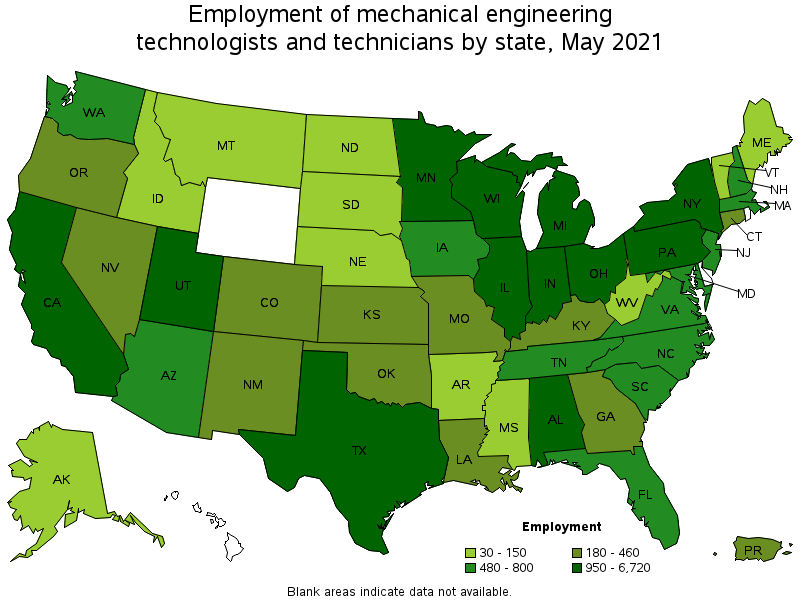
For tool and diemakers, four-year apprenticeship programs usually take place with employers. They receive training on the job from an experienced worker during their apprenticeship program. They can also take technical college courses at night. The program includes hands-on training, as well as classroom instruction. They also may have the opportunity to perform computer-controlled machine tool programming. They may also advance to supervisory positions.
A high school diploma is usually required for tool and die makers. They may also have a degree, such as in engineering or Physics. They might have also had training in science, math, or both. This training can be very helpful.
Good eyesight is essential for tool and die makers. They must be patient and have excellent concentration. They will also require physical strength to use machinery. They must have a strong work ethic, and be able to lift heavy loads. They should have the ability to read engineering drawings. They should have strong interpersonal skills. They should also be able to use computers effectively. They might be required to maintain computer numerically managed (CNC-) machines.
An analytical mind is essential for tool and die makers. They need to know how tools and their functions work, as well as how to repair them. They also need to be problem-solving and have mechanical aptitude. They may also have to learn new machining techniques. They should have substantial digital skills, such as computer-aided design (CAD) and computer-aided manufacturing (CAM) software. They should also have sales skills. They should be able collaborate with others and work independently.
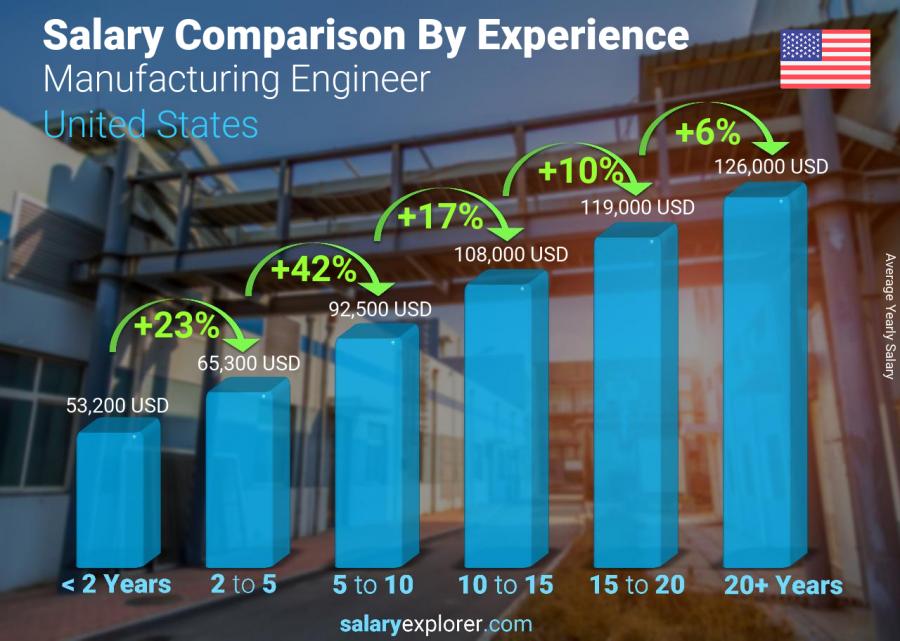
Apprentices usually work 40 hours per week in an apprenticeship program. Apprentices attend classes at night and then work during the day on a job. They take on more challenging tasks eventually. Most apprenticeships require a high school diploma or equivalent. They should also take courses in math and science.
Some tool and dentists go on to obtain a bachelor's (or master's) degree. The average tool and die maker's salary is $56,186. However, their job prospects are expected to decrease in the future due to automation.
FAQ
Why automate your warehouse
Modern warehousing has seen automation take center stage. With the rise of ecommerce, there is a greater demand for faster delivery times as well as more efficient processes.
Warehouses should be able adapt quickly to new needs. Technology investment is necessary to enable warehouses to respond quickly to changing demands. Automating warehouses has many benefits. These are just a few reasons to invest in automation.
-
Increases throughput/productivity
-
Reduces errors
-
Increases accuracy
-
Safety increases
-
Eliminates bottlenecks
-
Allows companies to scale more easily
-
Makes workers more efficient
-
It gives visibility to everything that happens inside the warehouse
-
Enhances customer experience
-
Improves employee satisfaction
-
It reduces downtime, and increases uptime
-
Quality products delivered on time
-
Eliminates human error
-
This helps to ensure compliance with regulations
What are the 7 Rs of logistics management?
The acronym "7R's" of Logistics stands for seven principles that underpin logistics management. It was developed by the International Association of Business Logisticians (IABL) and published in 2004 as part of its "Seven Principles of Logistics Management" series.
The acronym is made up of the following letters:
-
Responsible – ensure that all actions are legal and don't cause harm to anyone else.
-
Reliable - You can have confidence that you will fulfill your promises.
-
Be responsible - Use resources efficiently and avoid wasting them.
-
Realistic - Take into consideration all aspects of operations including cost-effectiveness, environmental impact, and other factors.
-
Respectful: Treat others with fairness and equity
-
Responsive - Look for ways to save time and increase productivity.
-
Recognizable - provide customers with value-added services.
What do we need to know about Manufacturing Processes in order to learn more about Logistics?
No. No. It is important to know about the manufacturing processes in order to understand how logistics works.
What are the differences between these four types?
Manufacturing refers to the transformation of raw materials into useful products by using machines and processes. It can involve many activities like designing, manufacturing, testing packaging, shipping, selling and servicing.
Statistics
- According to a Statista study, U.S. businesses spent $1.63 trillion on logistics in 2019, moving goods from origin to end user through various supply chain network segments. (netsuite.com)
- (2:04) MTO is a production technique wherein products are customized according to customer specifications, and production only starts after an order is received. (oracle.com)
- According to the United Nations Industrial Development Organization (UNIDO), China is the top manufacturer worldwide by 2019 output, producing 28.7% of the total global manufacturing output, followed by the United States, Japan, Germany, and India.[52][53] (en.wikipedia.org)
- It's estimated that 10.8% of the U.S. GDP in 2020 was contributed to manufacturing. (investopedia.com)
- Many factories witnessed a 30% increase in output due to the shift to electric motors. (en.wikipedia.org)
External Links
How To
How to Use Lean Manufacturing for the Production of Goods
Lean manufacturing (or lean manufacturing) is a style of management that aims to increase efficiency, reduce waste and improve performance through continuous improvement. It was first developed in Japan in the 1970s/80s by Taiichi Ahno, who was awarded the Toyota Production System (TPS), award from KanjiToyoda, the founder of TPS. Michael L. Watkins published the original book on lean manufacturing, "The Machine That Changed the World," in 1990.
Lean manufacturing is often described as a set if principles that help improve the quality and speed of products and services. It emphasizes reducing defects and eliminating waste throughout the value chain. Just-in-time (JIT), zero defect (TPM), and 5S are all examples of lean manufacturing. Lean manufacturing is about eliminating activities that do not add value, such as inspection, rework, and waiting.
In addition to improving product quality and reducing costs, lean manufacturing helps companies achieve their goals faster and reduces employee turnover. Lean manufacturing has been deemed one of the best ways to manage the entire value-chain, including customers, distributors as well retailers and employees. Lean manufacturing practices are widespread in many industries. Toyota's philosophy, for example, is what has enabled it to be successful in electronics, automobiles, medical devices, healthcare and chemical engineering as well as paper and food.
Lean manufacturing is based on five principles:
-
Define value - Find out what your business contributes to society, and what makes it different from other competitors.
-
Reduce Waste - Eliminate any activity that doesn't add value along the supply chain.
-
Create Flow. Ensure that your work is uninterrupted and flows seamlessly.
-
Standardize and simplify – Make processes as repeatable and consistent as possible.
-
Develop Relationships: Establish personal relationships both with internal and external stakeholders.
Lean manufacturing, although not new, has seen renewed interest in the economic sector since 2008. To increase their competitiveness, many businesses have turned to lean manufacturing. In fact, some economists believe that lean manufacturing will be an important factor in economic recovery.
Lean manufacturing is now becoming a common practice in the automotive industry, with many benefits. These include higher customer satisfaction, lower inventory levels, lower operating expenses, greater productivity, and improved overall safety.
It can be applied to any aspect of an organisation. However, it is particularly useful when applied to the production side of an organization because it ensures that all steps in the value chain are efficient and effective.
There are three types of lean manufacturing.
-
Just-in Time Manufacturing: This lean manufacturing method is commonly called "pull systems." JIT means that components are assembled at the time of use and not manufactured in advance. This approach is designed to reduce lead times and increase the availability of components. It also reduces inventory.
-
Zero Defects Manufacturing: ZDM ensures that no defective units leave the manufacturing plant. If a part needs to be fixed during the assembly line, it should be repaired rather than scrapped. This also applies to finished products that need minor repairs before being shipped.
-
Continuous Improvement (CI): CI aims to improve the efficiency of operations by continuously identifying problems and making changes in order to eliminate or minimize waste. Continuous Improvement (CI) involves continuous improvement in processes, people, tools, and infrastructure.