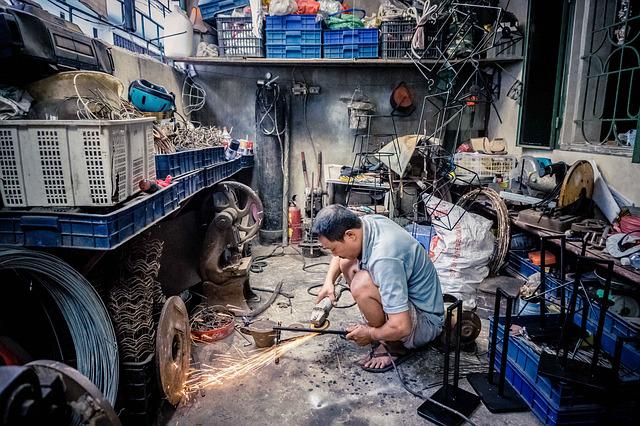
Typically, tool and die makers work in machine shops. They work with lathes and milling machines as well as other types. They can also repair dies and tools for machinists. They might also design tools for customers.
Tool and diemakers are required to adhere to high quality standards and maintain precision in their work. They inspect finished products and test their accuracy. To improve processes, tool- and die-makers can work with engineers. Sometimes they will travel to the customer's place to inspect how the tool works. They must also keep their work areas clean and organized. They may wear protective gear. They may suggest other tools to speed up the process.
The typical work week for tool and die makers is 40 hours. They might also be required to lift moderately heavy loads. They are also required to have a strong educational background. Employers often prefer applicants with an associate's (or bachelor's) degree in a related field. They might also be eligible for formal training on the job or apprenticeship programs.
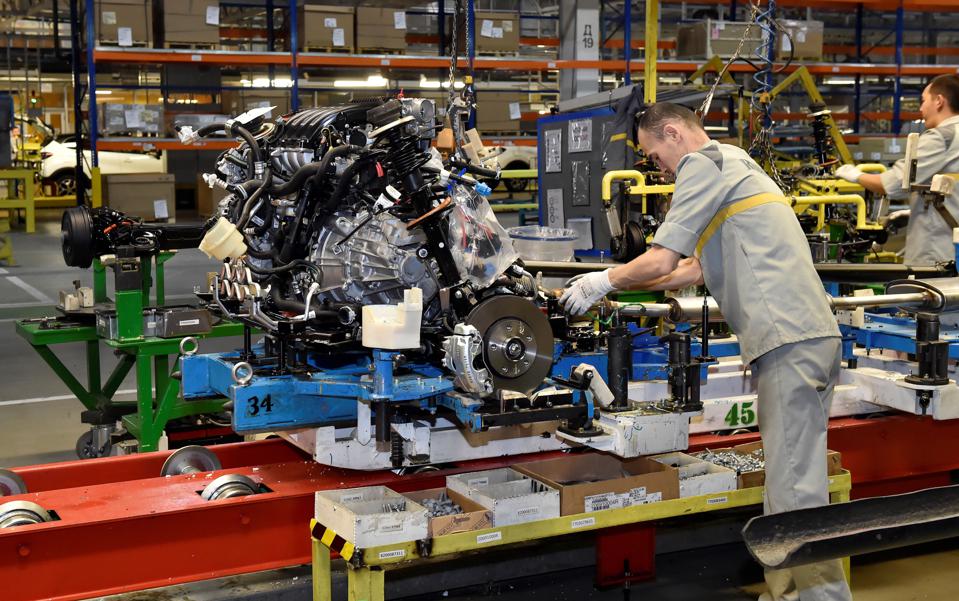
Tool and die makers typically attend four-year apprenticeship programs with employers. During the apprenticeship program, they receive on-the-job training from an experienced worker. They also receive technical college courses in the evening. The program includes hands-on training, as well as classroom instruction. They also may have the opportunity to perform computer-controlled machine tool programming. They could also be promoted to supervisory roles.
A high school diploma or equivalent is required for tool- and die-makers. They may also have a degree in a technical field, such as physics or engineering. They might have also had training in science, math, or both. This training is often beneficial.
Tool and die makers must have excellent eyesight. They must have good concentration and patience. They will also require physical strength to use machinery. They need to have a strong work ethic as well as the ability to lift heavy objects. They should be able and able to read technical drawings and specifications. They should also possess good interpersonal skills. They must have excellent computer skills. They may also need to be able to maintain computer numerically-controlled (CNC), machines.
A tool and die maker must be analytical. They must be able to comprehend how tools and dies function and how they can be repaired. They also have to have mechanical aptitude and problem-solving skills. They may also be required to learn new methods of machining. They will need to be proficient in digital skills like computer-aided planning (CAD) and computer aided manufacturing (CAM). They must also be able to sell. They must be able both to work alone and with others.
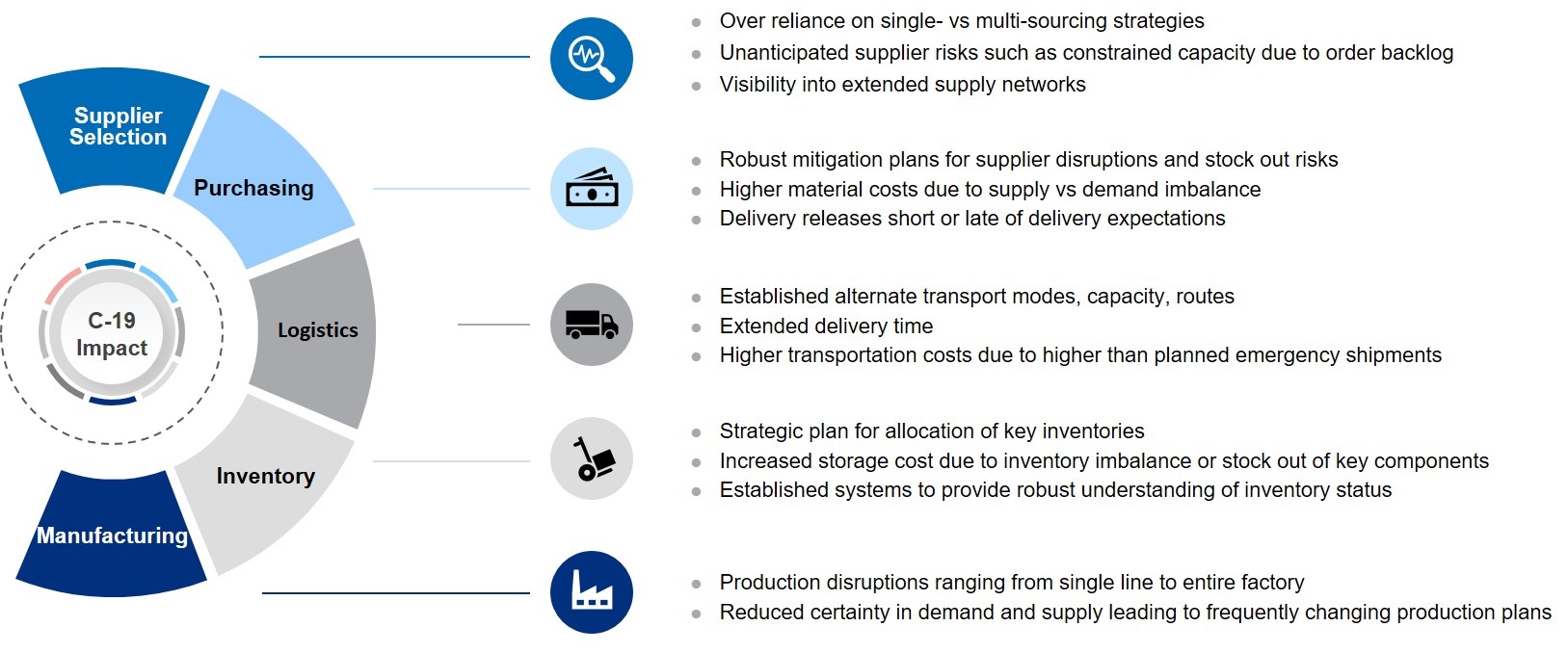
Apprentices usually work 40 hours per week in an apprenticeship program. They work in a classroom during the night, and they attend class at night. They eventually accept more challenging assignments. A high school diploma is required for most apprenticeships. They should also be able to learn science and math.
Some tool and die makers go on to earn a bachelor's or master's degree. The average wage for tool- and die-makers is $56,186. However, automation is predicted to lower their chances of finding work in the future.
FAQ
What kind of jobs are there in logistics?
Logistics can offer many different jobs. These are some of the jobs available in logistics:
-
Warehouse workers – They load, unload and transport pallets and trucks.
-
Transport drivers - These are people who drive trucks and trailers to transport goods or perform pick-ups.
-
Freight handlers are people who sort and pack freight into warehouses.
-
Inventory managers – These people oversee inventory at warehouses.
-
Sales representatives: They sell products to customers.
-
Logistics coordinators - They organize and plan logistics operations.
-
Purchasing agents: They are responsible for purchasing goods and services to support company operations.
-
Customer service agents - They answer phone calls and respond to emails.
-
Ship clerks - They issue bills and process shipping orders.
-
Order fillers - They fill orders based on what is ordered and shipped.
-
Quality control inspectors are responsible for inspecting incoming and outgoing products looking for defects.
-
Other - Logistics has many other job opportunities, including transportation supervisors, logistics specialists, and cargo specialists.
What makes a production planner different from a project manger?
The main difference between a production planner and a project manager is that a project manager is usually the person who plans and organizes the entire project, whereas a production planner is mainly involved in the planning stage of the project.
What is the responsibility of a logistics manager?
Logistics managers are responsible for ensuring that all goods arrive in perfect condition and on time. This is done by using his/her experience and knowledge of the company's products. He/she also needs to ensure adequate stock to meet demand.
What does warehouse mean?
A warehouse or storage facility is where goods are stored before they are sold. It can be either an indoor or outdoor space. In some cases, it may be a combination of both.
What skills is required for a production planner?
You must be flexible and organized to become a productive production planner. Effective communication with clients and colleagues is essential.
Statistics
- Many factories witnessed a 30% increase in output due to the shift to electric motors. (en.wikipedia.org)
- In 2021, an estimated 12.1 million Americans work in the manufacturing sector.6 (investopedia.com)
- According to a Statista study, U.S. businesses spent $1.63 trillion on logistics in 2019, moving goods from origin to end user through various supply chain network segments. (netsuite.com)
- Job #1 is delivering the ordered product according to specifications: color, size, brand, and quantity. (netsuite.com)
- According to the United Nations Industrial Development Organization (UNIDO), China is the top manufacturer worldwide by 2019 output, producing 28.7% of the total global manufacturing output, followed by the United States, Japan, Germany, and India.[52][53] (en.wikipedia.org)
External Links
How To
How to use 5S to increase Productivity in Manufacturing
5S stands in for "Sort", the "Set In Order", "Standardize", or "Separate". The 5S methodology was developed at Toyota Motor Corporation in 1954. It helps companies achieve higher levels of efficiency by improving their work environment.
This method has the basic goal of standardizing production processes to make them repeatable. This means that every day tasks such cleaning, sorting/storing, packing, and labeling can be performed. Workers can be more productive by knowing what to expect.
Implementing 5S requires five steps. These are Sort, Set In Order, Standardize. Separate. And Store. Each step requires a different action to increase efficiency. Sorting things makes it easier to find them later. Once you have placed items in an ordered fashion, you will put them together. Then, after you separate your inventory into groups, you store those groups in containers that are easy to access. Finally, label all containers correctly.
Employees need to reflect on how they do their jobs. Employees need to understand the reasons they do certain jobs and determine if there is a better way. To be successful in the 5S system, employees will need to acquire new skills and techniques.
The 5S Method not only improves efficiency, but it also helps employees to be more productive and happier. Once they start to notice improvements, they are motivated to keep working towards their goal of increasing efficiency.