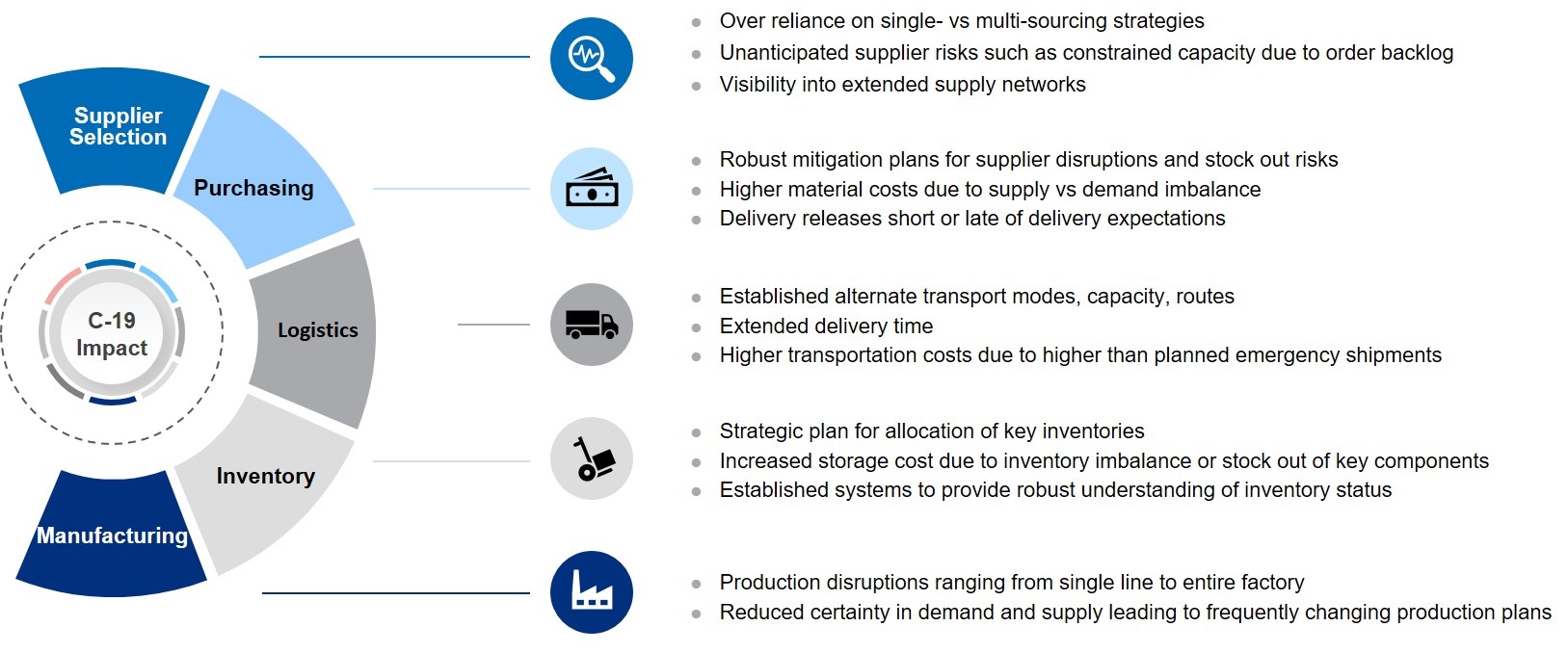
Assemblers is a low-level programming language often used in computers. Assemblers are closely linked to architecture machine code. Assemblers connect blocks of information together. This allows the assembler perform a variety of operations. The connection to machine code is the most fundamental and basic of all assemblers. It is crucial to use the correct syntax in order to write effective assembly codes.
Information about assemblers
Assemblers are software programs that can interpret assembly language and machine code. They allow application developers to manage hardware and access hardware resources, and are sometimes referred to as assembler compilers. This article will cover the basic functions of an assembler as well as the most widely used assemblers. Further, we will discuss the differences between assemblers and machine code. Let's examine the differences and see how assemblers differ to machine code.
Before you can use Assemblers, Inc., you need to register or create an account. This account can only be accessed by you. You are responsible to protect your password, account number, and log-in information. Assemblers, Inc. cannot be held responsible for your actions. You should immediately contact Assemblers, Inc. support if you are having problems with any program.
Functions for assemblers
An assembler, a program that converts the basic instructions for a computer into bits, is software. The processor executes those bits to perform basic computer functions. The assembler also converts bits to a mnemonic copy of the code. The output of an assembly program is known as an object programme. These can be interpreted and re-executed at will to accomplish specific tasks.
Assembler also performs memory bounds between addresses and names. The details of memory binding are not necessary for the programmer to understand. For the programmer to be able process the instructions correctly and provide the correct output, the assembly must be able do so. It also keeps machine-related information such as length, symbol, or pseudo-ops. This allows the compiler to identify exactly the instructions and data the program requires.
Syntax of assemblers
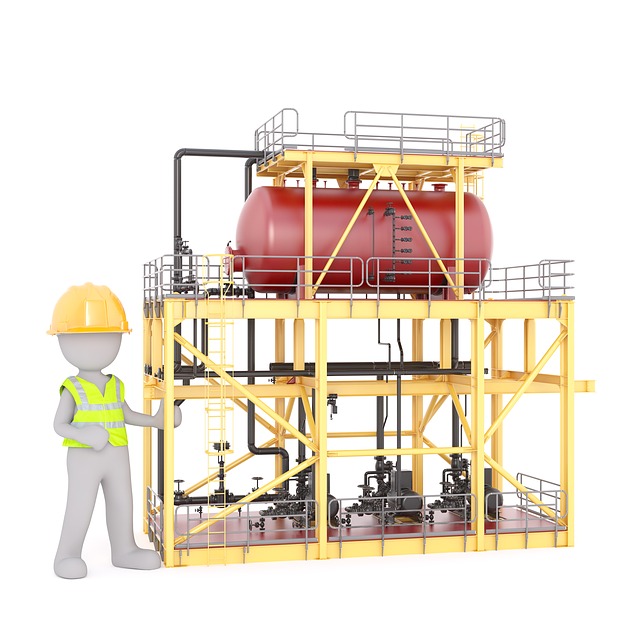
There are many ways that assemblers' syntax differs from that of disassemblers. First, they allow for the definition of macros. They may contain complex macro language with optional conditions, strings, and math operations. They may also allow for saving context and generate code not yet written in machine-language. Macros can also be used to support variable declarations as well as unrolled loops.
Assemblers can address in many different ways. Assemblers determine the format of addressing, which is different from other languages. Instructions, pseudoinstructions directives and symbolic register names must be written with uppercase. The comment must be included at the end of each source line. Comments are string literals and should not be placed on the exact same line as executable directions. Blank lines, while not essential, may make your code easier to understand.
Job prospects for assemblers
Assemblers or fabricators are responsible for assembling parts and final products. Many work in factories, and their duties may involve long periods of sitting or standing. It is usually a full-time job. However, education and experience requirements can vary from industry to industry. In May 2021, assembly and fabrication workers earned $37,170. Overall employment is expected to drop by five percent between 2020 and 2030. Although the demand for this job is expected to decline through 2020-2021, it is still a positive outlook.
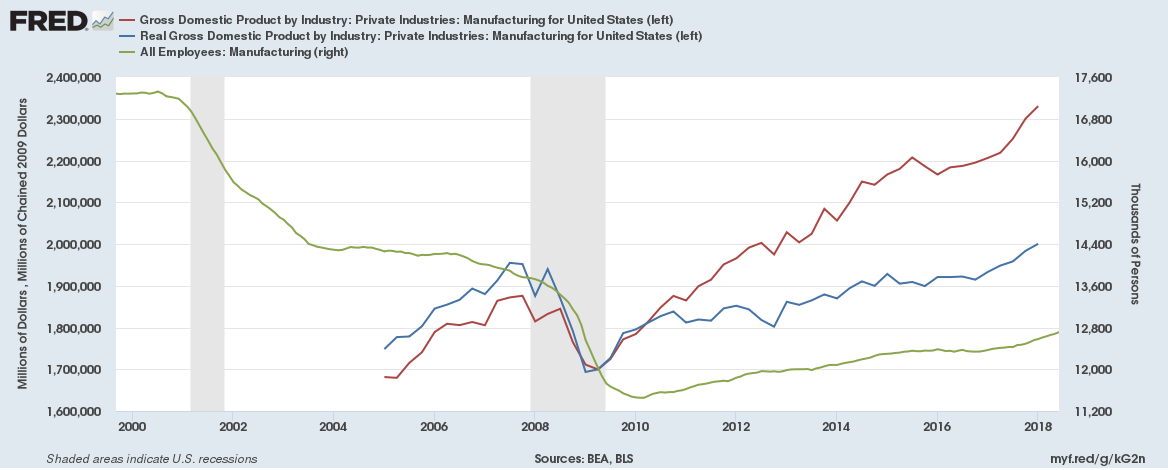
Assemblers follow a detailed plan to assemble parts. Assemblers follow a detailed plan and measure and cut the parts. These parts are then connected using bolts, screws, or welding. These workers are often responsible for special orders and quality control. They can use hand and power tools to accomplish their tasks. Assembly workers also perform general maintenance and cleaning duties. For a position as an assembly worker, you will need a high-school diploma.
FAQ
How can we increase manufacturing efficiency?
First, identify the factors that affect production time. The next step is to identify the most important factors that affect production time. If you don’t know where to begin, consider which factors have the largest impact on production times. Once you've identified them all, find solutions to each one.
How does a production planner differ from a project manager?
The primary difference between a producer planner and a manager of a project is that the manager usually plans and organizes the whole project, while a production planner is only involved in the planning stage.
How can manufacturing avoid production bottlenecks
Production bottlenecks can be avoided by ensuring that processes are running smoothly during the entire production process, starting with the receipt of an order and ending when the product ships.
This includes both quality control and capacity planning.
Continuous improvement techniques such Six Sigma are the best method to accomplish this.
Six Sigma can be used to improve the quality and decrease waste in all areas of your company.
It emphasizes consistency and eliminating variance in your work.
What is the distinction between Production Planning or Scheduling?
Production Planning (PP), is the process of deciding what production needs to take place at any given time. Forecasting and identifying production capacity are two key elements to this process.
Scheduling is the process of assigning specific dates to tasks so they can be completed within the specified timeframe.
How can manufacturing overproduction be reduced?
Improved inventory management is the key to reducing overproduction. This would reduce the time spent on unproductive activities like purchasing, storing and maintaining excess stock. This will allow us to free up resources for more productive tasks.
You can do this by adopting a Kanban method. A Kanban board is a visual display used to track work in progress. A Kanban system allows work items to move through several states before reaching their final destination. Each state has a different priority level.
As an example, if work is progressing from one stage of the process to another, then the current task is complete and can be transferred to the next. A task that is still in the initial stages of a process will be considered complete until it moves on to the next stage.
This allows work to move forward and ensures that no work is missed. Managers can monitor the work being done by Kanban boards to see what is happening at any given time. This allows them the ability to adjust their workflow using real-time data.
Lean manufacturing can also be used to reduce inventory levels. Lean manufacturing focuses on eliminating waste throughout the entire production chain. Anything that does nothing to add value to a product is waste. These are some of the most common types.
-
Overproduction
-
Inventory
-
Unnecessary packaging
-
Material surplus
These ideas will help manufacturers increase efficiency and lower costs.
Why is logistics important in manufacturing?
Logistics are an essential component of any business. They can help you achieve great success by helping you manage product flow from raw material to finished goods.
Logistics play an important role in reducing costs as well as increasing efficiency.
What does warehouse mean?
A warehouse is a place where goods are stored until they are sold. You can have it indoors or outdoors. It could be one or both.
Statistics
- In 2021, an estimated 12.1 million Americans work in the manufacturing sector.6 (investopedia.com)
- In the United States, for example, manufacturing makes up 15% of the economic output. (twi-global.com)
- (2:04) MTO is a production technique wherein products are customized according to customer specifications, and production only starts after an order is received. (oracle.com)
- According to the United Nations Industrial Development Organization (UNIDO), China is the top manufacturer worldwide by 2019 output, producing 28.7% of the total global manufacturing output, followed by the United States, Japan, Germany, and India.[52][53] (en.wikipedia.org)
- [54][55] These are the top 50 countries by the total value of manufacturing output in US dollars for its noted year according to World Bank.[56] (en.wikipedia.org)
External Links
How To
How to Use Lean Manufacturing in the Production of Goods
Lean manufacturing (or lean manufacturing) is a style of management that aims to increase efficiency, reduce waste and improve performance through continuous improvement. It was developed in Japan between 1970 and 1980 by Taiichi Ohno. TPS founder Kanji Tyoda gave him the Toyota Production System, or TPS award. The first book published on lean manufacturing was titled "The Machine That Changed the World" written by Michael L. Watkins and published in 1990.
Lean manufacturing is often defined as a set of principles used to improve the quality, speed, and cost of products and services. It emphasizes reducing defects and eliminating waste throughout the value chain. Lean manufacturing is called just-in-time (JIT), zero defect, total productive maintenance (TPM), or 5S. Lean manufacturing is about eliminating activities that do not add value, such as inspection, rework, and waiting.
Lean manufacturing improves product quality and costs. It also helps companies reach their goals quicker and decreases employee turnover. Lean manufacturing is a great way to manage the entire value chain including customers, suppliers, distributors and retailers as well as employees. Lean manufacturing is widely used in many industries. For example, Toyota's philosophy underpins its success in automobiles, electronics, appliances, healthcare, chemical engineering, aerospace, paper, food, etc.
Lean manufacturing includes five basic principles:
-
Define value - Find out what your business contributes to society, and what makes it different from other competitors.
-
Reduce Waste – Eliminate all activities that don't add value throughout the supply chain.
-
Create Flow - Ensure work moves smoothly through the process without interruption.
-
Standardize and Simplify – Make processes as consistent, repeatable, and as simple as possible.
-
Build Relationships- Develop personal relationships with both internal as well as external stakeholders.
Although lean manufacturing isn't a new concept in business, it has gained popularity due to renewed interest in the economy after the 2008 global financial crisis. Many businesses are now using lean manufacturing to improve their competitiveness. Some economists even believe that lean manufacturing can be a key factor in economic recovery.
Lean manufacturing has many benefits in the automotive sector. These include better customer satisfaction and lower inventory levels. They also result in lower operating costs.
Any aspect of an enterprise can benefit from Lean manufacturing. This is because it ensures efficiency and effectiveness in all stages of the value chain.
There are three types of lean manufacturing.
-
Just-in-Time Manufacturing (JIT): This type of lean manufacturing is commonly referred to as "pull systems." JIT stands for a system where components are assembled on the spot rather than being made in advance. This strategy aims to decrease lead times, increase availability of parts and reduce inventory.
-
Zero Defects Manufacturing, (ZDM): ZDM is focused on ensuring that no defective products leave the manufacturing facility. It is better to repair a part than have it removed from the production line if it needs to be fixed. This applies to finished products, which may need minor repairs before they are shipped.
-
Continuous Improvement (CI): CI aims to improve the efficiency of operations by continuously identifying problems and making changes in order to eliminate or minimize waste. Continuous improvement involves continuous improvement of processes and people as well as tools.