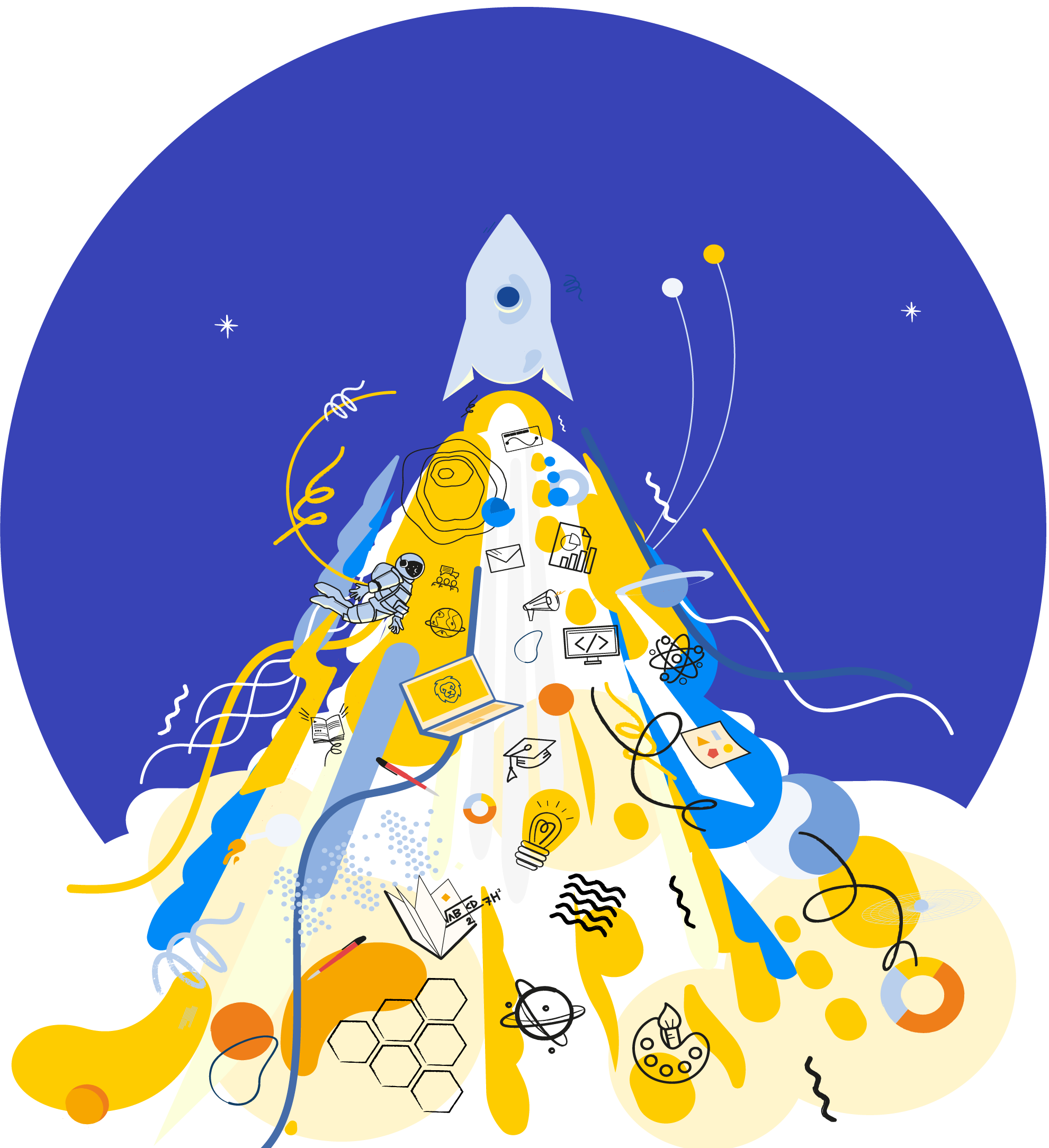
Companies can use lean product development methods to ensure products that are best suited for their customers' needs. Lean products can reduce waste and speed up product design. Companies can also remain competitive by using lean methods.
Lean product design is a combination of engineering and manufacturing. Its purpose, is to produce a working product using less time, stock and effort. It has rapid learning cycles and uses visual planning methods such as visual boards. It also integrates set based concurrent engineering.
Lean product development begins with understanding the customer. This involves understanding the customer and identifying the risks involved in the business plan. It is important to understand the scope of the product, which includes functions and features. If the customer doesn't use them, they can make the product more expensive and unnecessary. It also includes developing a verification and validation plan.
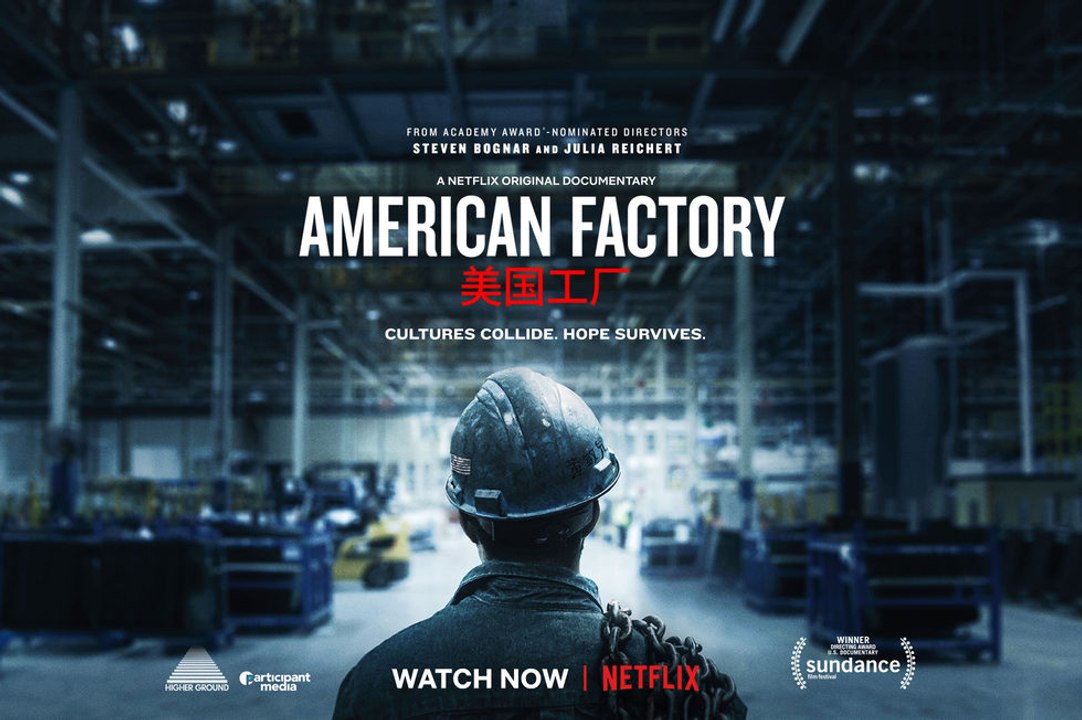
Next, you need to create an activity networking. This allows teams and individuals to set their own work and plan their work. The network provides a framework for the development of value. It reduces waste, and it helps teams identify opportunities to improve processes.
The ideal PD process focuses on a continuous flow of value from conception to production. It should not include bureaucratic stops and loop backs to correct any errors. It should be able to represent the entire value stream. The system should not be broken down or lead to systemic vision loss. This should be a one-piece flow in manufacturing.
The first step is to determine its value. This is done through an analysis of the business case and a systematic literature review. It is vital to define the value expectations from all stakeholders. It is also crucial to define product scope. This includes customer's value, features and functions. These are the elements that determine the technology and process used.
The next step in the process is to design the value flow. This involves identifying and eliminating any steps that don't contribute value to the value stream. Unused designs, untested code, and other inefficient steps should all be eliminated. Also, it is important to limit the number of tasks being done at once. This is often done by frequent changes to priorities.
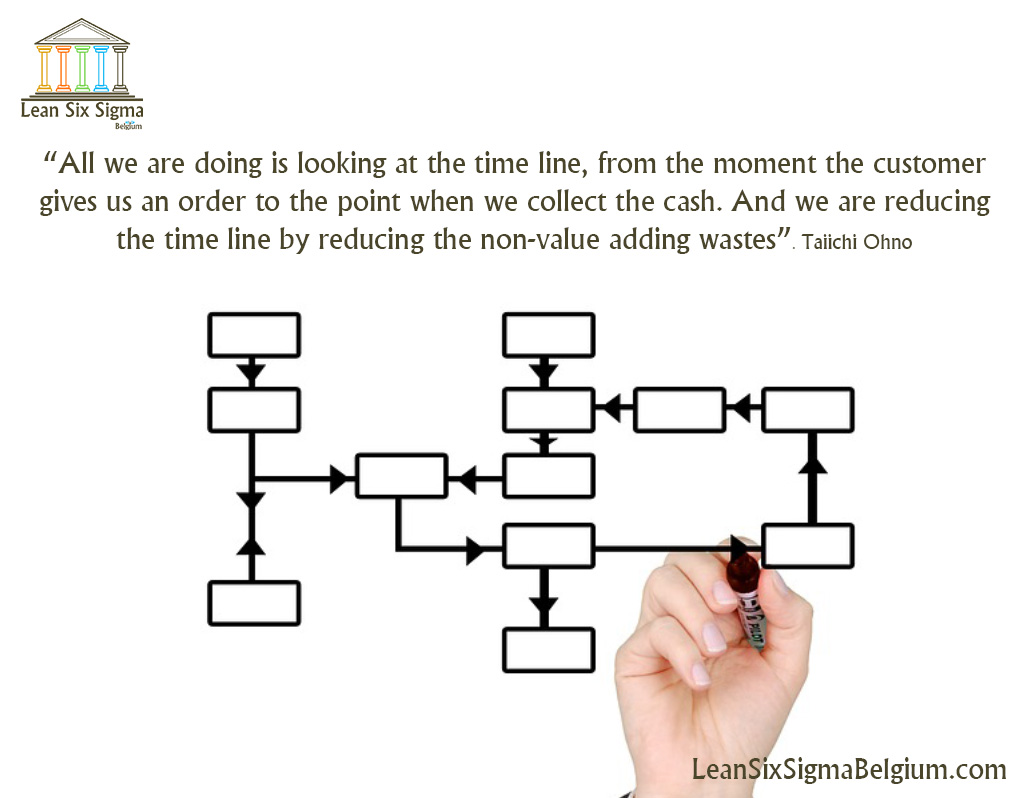
Lean product development can be a valuable tool for businesses that helps them reduce costs, identify inefficiencies and stay competitive. Lean product development allows companies to create sustainable value streams that will allow them to be profitable in the future. It has helped companies from all industries, including healthcare, high-tech and manufacturing.
Lean product design uses a set-based concurrent engineer approach to allow teams to develop products quicker and with fewer resources. Because of their complicated codebases, it took big companies longer to develop new products in the past than start-ups. This can be difficult to maintain and build upon.
FAQ
What is the role of a production manager?
Production planners ensure all aspects of the project are delivered within time and budget. They also ensure the quality of the product and service meets the client's requirements.
How can overproduction in manufacturing be reduced?
The key to reducing overproduction lies in developing better ways to manage inventory. This would reduce time spent on activities such as purchasing, stocking, and maintaining excess stock. This will allow us to free up resources for more productive tasks.
Kanban systems are one way to achieve this. A Kanban board can be used to monitor work progress. In a Kanban system, work items move through a sequence of states until they reach their final destination. Each state represents a different priority level.
To illustrate, work can move from one stage or another when it is complete enough for it to be moved to a new stage. However, if a task is still at the beginning stages, it will remain so until it reaches the end of the process.
This allows for work to continue moving forward, while also ensuring that there is no work left behind. Managers can monitor the work being done by Kanban boards to see what is happening at any given time. This information allows them to adjust their workflow based on real-time data.
Lean manufacturing is another way to manage inventory levels. Lean manufacturing is about eliminating waste from all stages of the production process. Anything that does not contribute to the product's value is considered waste. Some common types of waste include:
-
Overproduction
-
Inventory
-
Unnecessary packaging
-
Material surplus
By implementing these ideas, manufacturers can improve efficiency and cut costs.
What are manufacturing & logistics?
Manufacturing refers to the process of making goods using raw materials and machines. Logistics manages all aspects of the supply chain, including procurement, production planning and distribution, inventory control, transportation, customer service, and transport. Logistics and manufacturing are often referred to as one thing. It encompasses both the creation of products and their delivery to customers.
What does the term manufacturing industries mean?
Manufacturing Industries are companies that manufacture products. The people who buy these products are called consumers. These companies use a variety processes such as distribution, retailing and management to accomplish their purpose. They create goods from raw materials, using machines and various other equipment. This includes all types and varieties of manufactured goods, such as food items, clothings, building supplies, furnitures, toys, electronics tools, machinery vehicles, pharmaceuticals medical devices, chemicals, among others.
Statistics
- It's estimated that 10.8% of the U.S. GDP in 2020 was contributed to manufacturing. (investopedia.com)
- According to the United Nations Industrial Development Organization (UNIDO), China is the top manufacturer worldwide by 2019 output, producing 28.7% of the total global manufacturing output, followed by the United States, Japan, Germany, and India.[52][53] (en.wikipedia.org)
- [54][55] These are the top 50 countries by the total value of manufacturing output in US dollars for its noted year according to World Bank.[56] (en.wikipedia.org)
- Job #1 is delivering the ordered product according to specifications: color, size, brand, and quantity. (netsuite.com)
- According to a Statista study, U.S. businesses spent $1.63 trillion on logistics in 2019, moving goods from origin to end user through various supply chain network segments. (netsuite.com)
External Links
How To
Six Sigma in Manufacturing
Six Sigma is defined by "the application SPC (statistical process control) techniques to achieve continuous improvements." Motorola's Quality Improvement Department developed it at their Tokyo plant in Japan in 1986. Six Sigma's basic concept is to improve quality and eliminate defects through standardization. In recent years, many companies have adopted this method because they believe there is no such thing as perfect products or services. Six Sigma's main objective is to reduce variations from the production average. It is possible to measure the performance of your product against an average and find the percentage of time that it differs from the norm. If there is a significant deviation from the norm, you will know that something needs to change.
Understanding the dynamics of variability within your business is the first step in Six Sigma. Once you've understood that, you'll want to identify sources of variation. You'll also want to determine whether these variations are random or systematic. Random variations happen when people make errors; systematic variations are caused externally. Random variations would include, for example, the failure of some widgets to fall from the assembly line. However, if you notice that every time you assemble a widget, it always falls apart at exactly the same place, then that would be a systematic problem.
Once you've identified where the problems lie, you'll want to design solutions to eliminate those problems. You might need to change the way you work or completely redesign the process. You should then test the changes again after they have been implemented. If they didn't work, then you'll need to go back to the drawing board and come up with another plan.