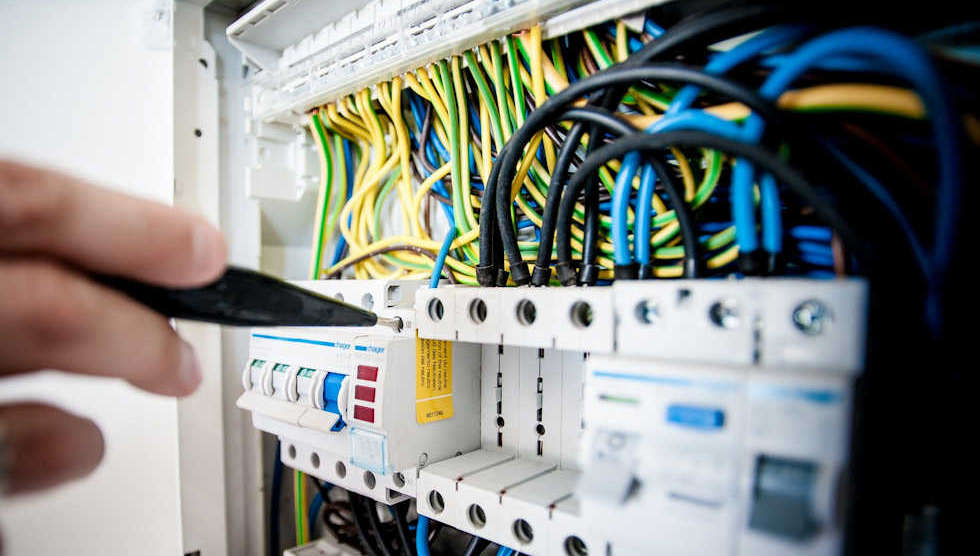
American Factory
In Ohio, the state is undergoing a post-industrial revolution. A Chinese millionaire hires 2000 Americans to reopen a factory. This creates new hope and promises. As high-tech China struggles to coexist with blue-collar American worker, a cultural clash results.
The Obamas now have their own production company, and they released this week a trailer of American Factory. It is a documentary on a Chinese factory which opens in an ex-General Motors plant in Ohio. The film is produced by Barack Obama's and Michelle Obama's Higher Ground production company and is scheduled to be released on Netflix August 21.
American Factory arrives just at the right time. Directed by Steven Bognar and Julia Reichert (The Last Truck: Closing of a GM Plant) and a winner of the Best Documentary title at the Sundance Film Festival, American Factory is a timely and compelling look at what happens when a long-shuttered factory is revitalized by a Chinese auto-glass manufacturer.
In 2014, when a Chinese manufacturer bought a shuttered General Motors factory outside Dayton in Ohio, the community felt a sense hope and promise. But the factory's arrival also brought with it a clash of cultures and a serious consideration of the prospects for unionization.
They wonder if, as they adjust to the Chinese work culture and expectations of their coworkers they will be able achieve their goals. They are also afraid of being labeled as "uncommitted," sloppy" or "inefficient."
One Chinese furnace operator, Wong He, talks about his work ethic and how he loves it, but it's hard to make a living in that kind of environment. He says he's working long hours with little time for his family.
He is a supporter of unionization and a member in the China Labor Alliance. But his boss doesn't want unions because it can make the company less efficient.
This is not the case in America, as management there is more focused on protecting its bottom-line. It's not a stance that most American workers agree with, but it's the way things are going for a lot of companies today.
It is important to understand the implications of this new stance. This means that it is not wise to be defensive in regards to your rights.
Many people in the United States feel like their power distance has been shrinking. The majority of Americans are willing to accept a job that doesn't demand them to be there all the times, or even to work for no pay.
This shift will have the greatest impact on the millennials, those born after 1990. They're a generation that's grown up with a one-child policy, and they have a strong desire for a life outside of work. They do not like being forced to work overtime and neither does their boss.
FAQ
How can manufacturing prevent production bottlenecks?
Avoiding production bottlenecks is as simple as keeping all processes running smoothly, from the time an order is received until the product ships.
This includes planning for both capacity requirements and quality control measures.
This can be done by using continuous improvement techniques, such as Six Sigma.
Six Sigma can be used to improve the quality and decrease waste in all areas of your company.
It seeks to eliminate variation and create consistency in your work.
Is it possible to automate certain parts of manufacturing
Yes! Yes. The Egyptians invented the wheel thousands of years ago. To help us build assembly lines, we now have robots.
There are many applications for robotics in manufacturing today. These include:
-
Automated assembly line robots
-
Robot welding
-
Robot painting
-
Robotics inspection
-
Robots that create products
Manufacturing could also benefit from automation in other ways. 3D printing makes it possible to produce custom products in a matter of days or weeks.
What is the role of a logistics manager
Logistics managers make sure all goods are delivered on schedule and without damage. This is done using his/her knowledge of the company's products. He/she should also ensure enough stock is available to meet demand.
What are the products and services of logistics?
Logistics refers to all activities that involve moving goods from A to B.
They cover all aspects of transportation, such as packing, loading, transporting and unloading.
Logisticians ensure the product reaches its destination in the most efficient manner. They provide information on demand forecasts as well stock levels, production schedules and availability of raw material.
They can also track shipments in transit and monitor quality standards.
How can excess manufacturing production be reduced?
The key to reducing overproduction lies in developing better ways to manage inventory. This would reduce the time needed to manage inventory. This could help us free up our time for other productive tasks.
You can do this by adopting a Kanban method. A Kanban board, a visual display to show the progress of work, is called a Kanban board. Work items are moved through various states to reach their destination in a Kanban system. Each state has a different priority level.
To illustrate, work can move from one stage or another when it is complete enough for it to be moved to a new stage. But if a task remains in the beginning stages it will stay that way until it reaches its end.
This keeps work moving and ensures no work is lost. With a Kanban board, managers can see exactly how much work is being done at any given moment. This allows them to adjust their workflows based on real-time information.
Lean manufacturing is another option to control inventory levels. Lean manufacturing focuses on eliminating waste throughout the entire production chain. Anything that does nothing to add value to a product is waste. Here are some examples of common types.
-
Overproduction
-
Inventory
-
Packaging that is not necessary
-
Excess materials
These ideas will help manufacturers increase efficiency and lower costs.
Is there anything we should know about Manufacturing Processes prior to learning about Logistics.
No. No. Understanding the manufacturing process will allow you to better understand logistics.
Statistics
- (2:04) MTO is a production technique wherein products are customized according to customer specifications, and production only starts after an order is received. (oracle.com)
- According to the United Nations Industrial Development Organization (UNIDO), China is the top manufacturer worldwide by 2019 output, producing 28.7% of the total global manufacturing output, followed by the United States, Japan, Germany, and India.[52][53] (en.wikipedia.org)
- According to a Statista study, U.S. businesses spent $1.63 trillion on logistics in 2019, moving goods from origin to end user through various supply chain network segments. (netsuite.com)
- Many factories witnessed a 30% increase in output due to the shift to electric motors. (en.wikipedia.org)
- In 2021, an estimated 12.1 million Americans work in the manufacturing sector.6 (investopedia.com)
External Links
How To
How to Use Lean Manufacturing in the Production of Goods
Lean manufacturing is a management style that aims to increase efficiency and reduce waste through continuous improvement. It was developed in Japan between 1970 and 1980 by Taiichi Ohno. TPS founder Kanji Tyoda gave him the Toyota Production System, or TPS award. Michael L. Watkins published the original book on lean manufacturing, "The Machine That Changed the World," in 1990.
Lean manufacturing is often defined as a set of principles used to improve the quality, speed, and cost of products and services. It is about eliminating defects and waste from all stages of the value stream. Lean manufacturing is called just-in-time (JIT), zero defect, total productive maintenance (TPM), or 5S. Lean manufacturing eliminates non-value-added tasks like inspection, rework, waiting.
Lean manufacturing improves product quality and costs. It also helps companies reach their goals quicker and decreases employee turnover. Lean manufacturing is considered one of the most effective ways to manage the entire value chain, including suppliers, customers, distributors, retailers, and employees. Many industries worldwide use lean manufacturing. For example, Toyota's philosophy underpins its success in automobiles, electronics, appliances, healthcare, chemical engineering, aerospace, paper, food, etc.
Lean manufacturing is based on five principles:
-
Define Value - Determine the value that your business brings to society. Also, identify what sets you apart from your competitors.
-
Reduce Waste – Eliminate all activities that don't add value throughout the supply chain.
-
Create Flow – Ensure that work flows smoothly throughout the process.
-
Standardize and simplify – Make processes as repeatable and consistent as possible.
-
Building Relationships – Establish personal relationships with both external and internal stakeholders.
Although lean manufacturing isn't a new concept in business, it has gained popularity due to renewed interest in the economy after the 2008 global financial crisis. To increase their competitiveness, many businesses have turned to lean manufacturing. Economists think that lean manufacturing is a crucial factor in economic recovery.
Lean manufacturing is now becoming a common practice in the automotive industry, with many benefits. These include better customer satisfaction and lower inventory levels. They also result in lower operating costs.
You can apply Lean Manufacturing to virtually any aspect of your organization. However, it is particularly useful when applied to the production side of an organization because it ensures that all steps in the value chain are efficient and effective.
There are three main types of lean manufacturing:
-
Just-in Time Manufacturing (JIT), also known as "pull system": This form of lean manufacturing is often referred to simply as "pull". JIT is a process in which components can be assembled at the point they are needed, instead of being made ahead of time. This method reduces lead times, increases availability, and decreases inventory.
-
Zero Defects Manufacturing (ZDM): ZDM focuses on ensuring that no defective units leave the manufacturing facility. If a part needs to be fixed during the assembly line, it should be repaired rather than scrapped. This is true even for finished products that only require minor repairs prior to shipping.
-
Continuous Improvement (CI),: Continuous improvement aims improve the efficiency and effectiveness of operations by continuously identifying issues and making changes to reduce waste. Continuous Improvement involves continuous improvement of processes.