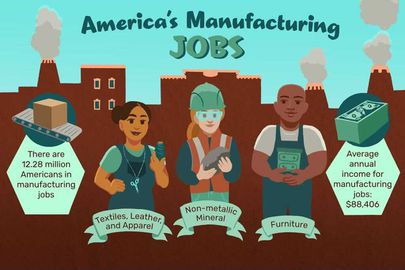
As nuclear technicians, you are responsible for maintaining and monitoring equipment and machines that are used in the production and testing of nuclear energy. A nuclear technician typically works at a power plant. They can gain more responsibility as they get experience. They can perform radiation tests and troubleshoot equipment.
You will need an associate's or bachelor's degree to become a nuclear technician. You will also need to take training. Most employers require two years of specialized training to qualify for a nuclear technician job. Once you have completed your training, you will be eligible for positions as a nuclear technician in a power plant or laboratory. You can also specialize as a nuclear waste manager and become an engineer.
A nuclear technician typically works with scientists in nuclear energy research or production. They may also monitor and record radiation levels in nuclear reactors. In addition, nuclear technicians may operate specialized equipment, such as remote-control instrument panels. They also instruct staff regarding radiation safety procedures.
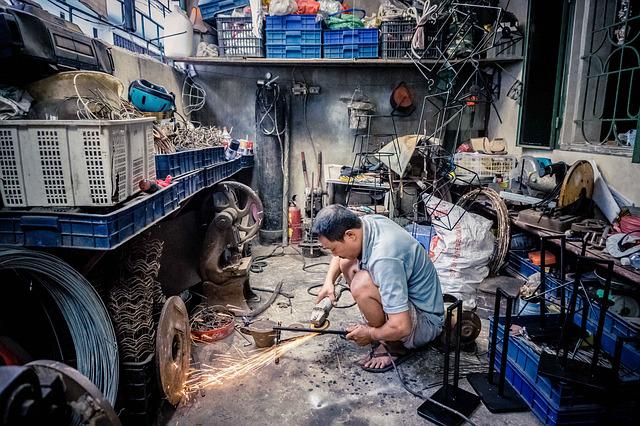
Additional to the general duties of a nuclear technician, they may be skilled in radiation protection or waste management. Some nuclear technicians might be required to have security clearance. They may also need to take advanced science and math courses.
You may also be eligible to apply for government jobs as a nuclear technician. These jobs require you to be able to think creatively, search for facts, and decipher complicated situations. The average hourly salary for a nuclear technician may be $38,10, but this is not the case.
A nuclear technician can also be a technical specialist. They may also earn more if they advance to higher levels of responsibility. This job is attractive because it offers high pay in many industries.
Nuclear technicians' salaries vary depending on their education and previous experience. You can expect to earn $31,000 an year as an entry-level technician. However, nuclear technicians who are experienced may be paid $115,000. This field is expected to grow at a rapid pace over the next 10 year. As a result, there should be approximately 1,400 new openings in this field.
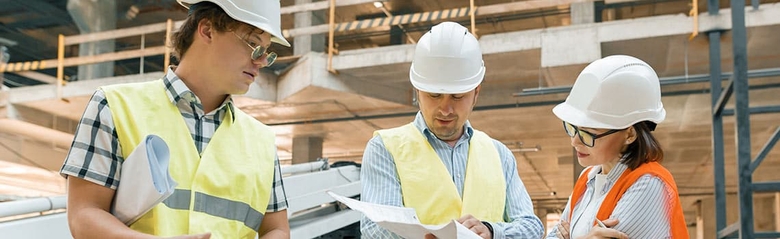
The salaries of nuclear technicians can vary from one place to the next. For instance, the average Illinois salary is $121,020 annually. California has the highest average salary for a Nuclear Technician. The national average salary is $126,000. This can vary from one state or another. Higher salaries might be offered to those who hold advanced degrees or have a degree as a nuclear technician.
While the Nuclear Technician's salary is among the most high-paying, it does NOT mean this career is the best. A passion for science and the ability think critically are essential. Also, you'll need to know how to operate specialized machinery. Many nuclear technicians seek further education to become certified.
FAQ
How can manufacturing excess production be decreased?
Better inventory management is key to reducing excess production. This would reduce the time spent on unproductive activities like purchasing, storing and maintaining excess stock. This will allow us to free up resources for more productive tasks.
Kanban systems are one way to achieve this. A Kanban Board is a visual display that tracks work progress. Work items are moved through various states to reach their destination in a Kanban system. Each state represents a different priority.
As an example, if work is progressing from one stage of the process to another, then the current task is complete and can be transferred to the next. However, if a task is still at the beginning stages, it will remain so until it reaches the end of the process.
This keeps work moving and ensures no work is lost. A Kanban board allows managers to monitor how much work is being completed at any given moment. This information allows them to adjust their workflow based on real-time data.
Another way to control inventory levels is to implement lean manufacturing. Lean manufacturing works to eliminate waste throughout every stage of the production chain. Anything that does not contribute to the product's value is considered waste. These are some of the most common types.
-
Overproduction
-
Inventory
-
Unnecessary packaging
-
Excess materials
These ideas can help manufacturers improve efficiency and reduce costs.
Is automation important for manufacturing?
Not only are service providers and manufacturers important, but so is automation. It enables them to provide services faster and more efficiently. In addition, it helps them reduce costs by reducing human errors and improving productivity.
What is the job of a manufacturer manager?
Manufacturing managers must ensure that manufacturing processes are efficient, effective, and cost-effective. They should be aware of any issues within the company and respond accordingly.
They should also be able and comfortable communicating with other departments like sales and marketing.
They should also be knowledgeable about the latest trends in the industry so they can use this information for productivity and efficiency improvements.
What type of jobs is there in logistics
There are many jobs available in logistics. Some examples are:
-
Warehouse workers – They load, unload and transport pallets and trucks.
-
Transport drivers - These are people who drive trucks and trailers to transport goods or perform pick-ups.
-
Freight handlers, - They sort out and pack freight in warehouses.
-
Inventory managers - These are responsible for overseeing the stock of goods in warehouses.
-
Sales representatives: They sell products to customers.
-
Logistics coordinators: They plan and manage logistics operations.
-
Purchasing agents: They are responsible for purchasing goods and services to support company operations.
-
Customer service agents - They answer phone calls and respond to emails.
-
Shippers clerks - They process shipping order and issue bills.
-
Order fillers: They fill orders based off what has been ordered and shipped.
-
Quality control inspectors – They inspect incoming and outgoing products to ensure that there are no defects.
-
Others – There are many other types available in logistics. They include transport supervisors, cargo specialists and others.
Statistics
- It's estimated that 10.8% of the U.S. GDP in 2020 was contributed to manufacturing. (investopedia.com)
- You can multiply the result by 100 to get the total percent of monthly overhead. (investopedia.com)
- According to a Statista study, U.S. businesses spent $1.63 trillion on logistics in 2019, moving goods from origin to end user through various supply chain network segments. (netsuite.com)
- Job #1 is delivering the ordered product according to specifications: color, size, brand, and quantity. (netsuite.com)
- [54][55] These are the top 50 countries by the total value of manufacturing output in US dollars for its noted year according to World Bank.[56] (en.wikipedia.org)
External Links
How To
Six Sigma in Manufacturing
Six Sigma is defined as "the application of statistical process control (SPC) techniques to achieve continuous improvement." Motorola's Quality Improvement Department created Six Sigma at their Tokyo plant, Japan in 1986. Six Sigma's basic concept is to improve quality and eliminate defects through standardization. Many companies have adopted this method in recent years. They believe there is no such thing a perfect product or service. Six Sigma seeks to reduce variation between the mean production value. This means that if you take a sample of your product, then measure its performance against the average, you can find out what percentage of the time the process deviates from the norm. If this deviation is too big, you know something needs fixing.
Understanding how variability works in your company is the first step to Six Sigma. Once you have this understanding, you will need to identify sources and causes of variation. You'll also want to determine whether these variations are random or systematic. Random variations occur when people make mistakes; systematic ones are caused by factors outside the process itself. For example, if you're making widgets, and some of them fall off the assembly line, those would be considered random variations. You might notice that your widgets always fall apart at the same place every time you put them together.
Once you've identified where the problems lie, you'll want to design solutions to eliminate those problems. That solution might involve changing the way you do things or redesigning the process altogether. After implementing the new changes, you should test them again to see if they worked. If they don’t work, you’ll need to go back and rework the plan.