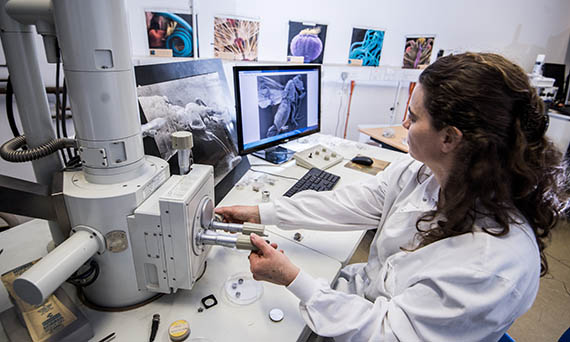
The Jacksonville, Florida area has a growing need for logistic jobs. These positions are crucial in the transportation and distribution of goods from factory floor to customer's doorstep. If you are a skilled worker, you can earn a good salary. Here are some tips and techniques to help you get the job you want.
It is a good idea to create a Monster account as the first step. You'll have access to job alerts and a customized list of related listings. You will also get expert advice. A savvy recruiter will even take the time to explain the perks of working for a certain company, so you'll be armed and ready to slay the competition. It's easy to get the job done if you know what your qualifications are and how they relate to the job you are applying for.
Consider a paid internship while you're at work. You'll learn the skills necessary to work with professionals for $10-15 an hour. In addition, you'll have real-world experiences that you can put to use when you search for a job. This is one of the most valuable types of training. A swag bag with goodies will reward you.
It is important to remember that you don’t need to be a logistician to get the job of your dreams. There are many opportunities for entry-level logistics professionals with no frills. Vaco and Penske both offer traditional work environments while others offer flexible options. Whatever route you decide to take, you'll likely find a suitable position in the Jacksonville, FL area.
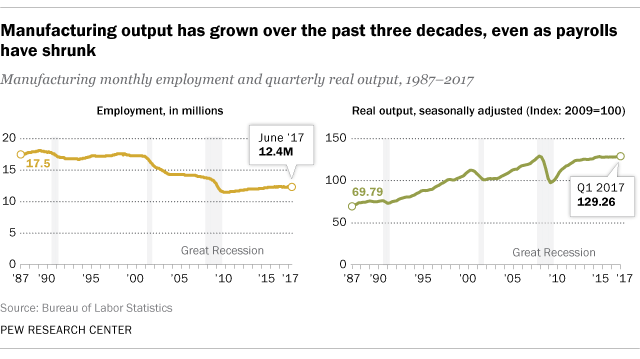
Scott Logistics Corp. and Quaker Transportation are two of the best companies in the region to get you started. Both are 3PLs, which is third-party logistics providers. They will give you the chance to experience what it's like working for a large company. Then, you'll be in a position to choose the one that suits you best. After all, you wouldn't want to miss out on a lucrative career just because you didn't know where to look.
FAQ
How does manufacturing avoid bottlenecks in production?
To avoid production bottlenecks, ensure that all processes run smoothly from the moment you receive your order to the time the product ships.
This includes planning to meet capacity requirements and quality control.
The best way to do this is to use continuous improvement techniques such as Six Sigma.
Six Sigma management is a system that improves quality and reduces waste within your organization.
It is focused on creating consistency and eliminating variation in your work.
What are the main products of logistics?
Logistics refers to all activities that involve moving goods from A to B.
They encompass all aspects transport, including packaging and loading, transporting, storage, unloading.
Logisticians ensure that the right product reaches the right place at the right time and under safe conditions. Logisticians assist companies in managing their supply chains by providing information such as demand forecasts, stock levels and production schedules.
They can also track shipments in transit and monitor quality standards.
What are the jobs in logistics?
There are different kinds of jobs available in logistics. Here are some examples:
-
Warehouse workers - They load trucks and pallets.
-
Transportation drivers - They drive trucks and trailers to deliver goods and carry out pick-ups.
-
Freight handlers are people who sort and pack freight into warehouses.
-
Inventory managers: They are responsible for the inventory and management of warehouses.
-
Sales representatives - They sell products.
-
Logistics coordinators – They plan and coordinate logistics operations.
-
Purchasing agents are those who purchase goods and services for the company.
-
Customer service representatives - They answer calls and emails from customers.
-
Shipping clerks – They process shipping orders, and issue bills.
-
Order fillers: They fill orders based off what has been ordered and shipped.
-
Quality control inspectors – They inspect incoming and outgoing products to ensure that there are no defects.
-
Others - There are many other types of jobs available in logistics, such as transportation supervisors, cargo specialists, etc.
What is production planning?
Production Planning refers to the development of a plan for every aspect of production. This document is designed to make sure everything is ready for when you're ready to shoot. You should also have information to ensure the best possible results on set. It should include information about shooting locations, casting lists, crew details, equipment requirements, and shooting schedules.
It is important to first outline the type of film you would like to make. You may already know where you want the film to be shot, or perhaps you have specific locations and sets you wish to use. Once you have determined your scenes and locations, it is time to start figuring out the elements that you will need for each scene. If you decide you need a car and don't know what model to choose, this could be an example. To narrow your options, you can search online for available models.
After you've found the perfect car, it's time to start thinking about adding extras. Do you need people sitting in the front seats? Or perhaps you need someone walking around the back of the car? You might want to change your interior color from black and white. These questions will help to determine the style and feel of your car. Also, think about what kind of shots you would like to capture. Are you going to be shooting close-ups? Or wide angles? Maybe you want to show your engine or the steering wheel. All of these things will help you identify the exact style of car you want to film.
Once you have made all the necessary decisions, you can start to create a schedule. You can create a schedule that will outline when you must start and finish your shoots. The schedule will show you when to get there, what time to leave, and when to return home. Everyone knows exactly what they should do and when. Book extra staff ahead of time if you need them. You don't want to hire someone who won't show up because he didn't know.
It is important to calculate the amount of filming days when you are creating your schedule. Some projects only take one or two days, while others may last weeks. It is important to consider whether you require more than one photo per day when you create your schedule. Multiple takes of the same location will lead to higher costs and take more time. It is better to be cautious and take fewer shots than you risk losing money if you are not sure if multiple takes are necessary.
Budget setting is an important part of production planning. You will be able to manage your resources if you have a realistic budget. Remember that you can always reduce the budget later on if you run into unforeseen problems. However, you shouldn't overestimate the amount of money you will spend. You will end up spending less money if you underestimate the cost of something.
Production planning is a very detailed process, but once you understand how everything works together, it becomes easier to plan future projects.
Why automate your warehouse?
Modern warehousing has seen automation take center stage. Increased demand for efficient and faster delivery has resulted in a rise in e-commerce.
Warehouses need to adapt quickly to meet changing needs. In order to do this, they need to invest in technology. Automating warehouses has many benefits. Here are some reasons why it's worth investing in automation:
-
Increases throughput/productivity
-
Reduces errors
-
Increases accuracy
-
Safety enhancements
-
Eliminates bottlenecks
-
Companies can scale more easily
-
Workers are more productive
-
Gives you visibility into all that is happening in your warehouse
-
Enhances customer experience
-
Improves employee satisfaction
-
Reducing downtime and increasing uptime
-
High quality products delivered on-time
-
Human error can be eliminated
-
This helps to ensure compliance with regulations
Statistics
- According to the United Nations Industrial Development Organization (UNIDO), China is the top manufacturer worldwide by 2019 output, producing 28.7% of the total global manufacturing output, followed by the United States, Japan, Germany, and India.[52][53] (en.wikipedia.org)
- According to a Statista study, U.S. businesses spent $1.63 trillion on logistics in 2019, moving goods from origin to end user through various supply chain network segments. (netsuite.com)
- Job #1 is delivering the ordered product according to specifications: color, size, brand, and quantity. (netsuite.com)
- Many factories witnessed a 30% increase in output due to the shift to electric motors. (en.wikipedia.org)
- In 2021, an estimated 12.1 million Americans work in the manufacturing sector.6 (investopedia.com)
External Links
How To
How to use Lean Manufacturing in the production of goods
Lean manufacturing is a management style that aims to increase efficiency and reduce waste through continuous improvement. It was developed by Taiichi Okono in Japan, during the 1970s & 1980s. TPS founder Kanji Takoda awarded him the Toyota Production System Award (TPS). Michael L. Watkins published the book "The Machine That Changed the World", which was the first to be published about lean manufacturing.
Lean manufacturing can be described as a set or principles that are used to improve quality, speed and cost of products or services. It emphasizes reducing defects and eliminating waste throughout the value chain. Just-in-time (JIT), zero defect (TPM), and 5S are all examples of lean manufacturing. Lean manufacturing focuses on eliminating non-value-added activities such as rework, inspection, and waiting.
Lean manufacturing can help companies improve their product quality and reduce costs. Additionally, it helps them achieve their goals more quickly and reduces employee turnover. Lean manufacturing is a great way to manage the entire value chain including customers, suppliers, distributors and retailers as well as employees. Lean manufacturing can be found in many industries. Toyota's philosophy has been a key driver of success in many industries, including automobiles and electronics.
Lean manufacturing includes five basic principles:
-
Define Value - Identify the value your business adds to society and what makes you different from competitors.
-
Reduce Waste - Eliminate any activity that doesn't add value along the supply chain.
-
Create Flow: Ensure that the work process flows without interruptions.
-
Standardize & Simplify - Make processes as consistent and repeatable as possible.
-
Build Relationships - Establish personal relationships with both internal and external stakeholders.
Lean manufacturing isn’t new, but it has seen a renewed interest since 2008 due to the global financial crisis. Many businesses have adopted lean production techniques to make them more competitive. Economists think that lean manufacturing is a crucial factor in economic recovery.
With many benefits, lean manufacturing is becoming more common in the automotive industry. These include improved customer satisfaction, reduced inventory levels, lower operating costs, increased productivity, and better overall safety.
The principles of lean manufacturing can be applied in almost any area of an organization. However, it is particularly useful when applied to the production side of an organization because it ensures that all steps in the value chain are efficient and effective.
There are three types of lean manufacturing.
-
Just-in Time Manufacturing, (JIT): This kind of lean manufacturing is also commonly known as "pull-systems." JIT refers to a system in which components are assembled at the point of use instead of being produced ahead of time. This strategy aims to decrease lead times, increase availability of parts and reduce inventory.
-
Zero Defects Manufacturing (ZDM): ZDM focuses on ensuring that no defective units leave the manufacturing facility. You should repair any part that needs to be repaired during an assembly line. This also applies to finished products that need minor repairs before being shipped.
-
Continuous Improvement (CI: Continuous improvement aims to increase the efficiency of operations by constantly identifying and making improvements to reduce or eliminate waste. Continuous improvement involves continuous improvement of processes and people as well as tools.