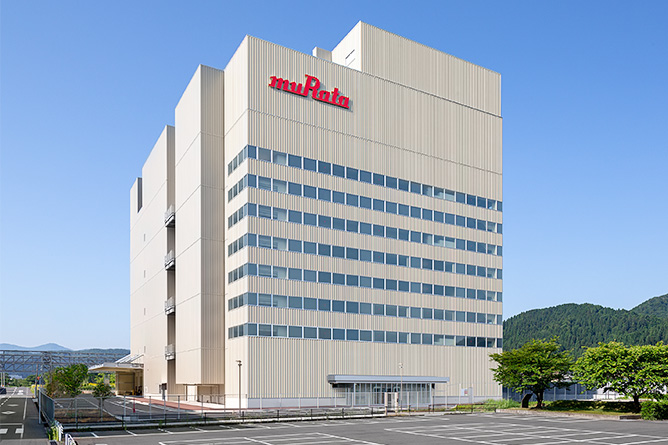
Planning demand is the process of predicting what future demand will be for a particular product or service. It is an integral part of the supply chain management process, because it helps businesses meet customers' demands while maximizing efficiency and profits.
What is Demand Planning?
Planning demand involves analyzing data, including sales data and inventory information, to forecast future demand for a given product or service. It is a complex process that can involve many different departments within a business.
What is Demand Planner?
A demand planner is a member of a company's supply chain team who uses their understanding of the industry and their business acumen to predict future market trends and customer needs. They create a detailed demand plan, which includes the best inventory levels and shipping schedules.
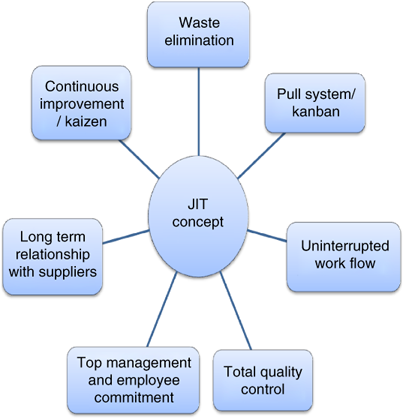
What are the best tools for demand planning?
The most effective demand planning tools are those that provide end-to-end visibility across a company's entire supply chain. The demand planners are then able to track the demand and analyze it in real-time.
How can I predict demand the most accurately?
Sales data is often directly provided by the sales team of a company. This is a good way to predict demand. This data can help you pinpoint any issues that your sales team might be having with their customers, which could lead to changes in your demand plan.
A statistical analysis can be used to establish the relationship between sales and inventories. Analyzing these relationships will improve the accuracy of your demand plan.
What are the most common mistakes in demand planning?
Demand planning requires a great deal of time and work to be successful. Demand planning can go wrong in a variety of ways. For example, excess inventory can lock up working capital, or increase inventory carrying costs. These can both cost money to the company and have a negative impact on customers.
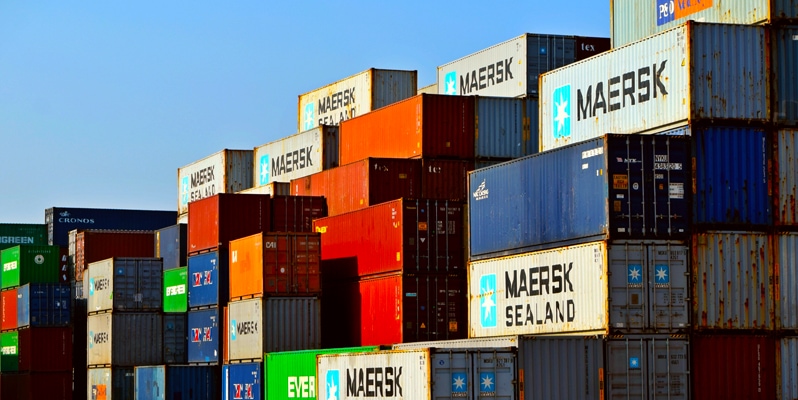
What are the most common skills that a demand planner requires?
A demand planner must have excellent analytical and managerial skills. They must have the ability to analyze complex data and take sound decisions on the basis of their findings. Also, they should be able work with other people and reach consensus.
What Are Some of the Most Valuable Skills in Demand Planning?
A great demand planner should be skilled with both people and technology. As they will be working closely with different teams on developing a forecasting tool, they should be able effectively communicate with them.
In addition to analyzing a wide range of statistical data, a demand planner should be skilled with the Delphi method, which allows them to solicit feedback from outside experts or facilitators who are not inside the company. This method comes in handy when there is a limited amount of data, and you are looking for more perspectives.
FAQ
What kind of jobs are there in logistics?
Logistics can offer many different jobs. Some examples are:
-
Warehouse workers - They load and unload trucks and pallets.
-
Transportation drivers: They drive trucks and trailers and deliver goods and make pick-ups.
-
Freight handlers – They sort and package freight at warehouses.
-
Inventory managers: They are responsible for the inventory and management of warehouses.
-
Sales reps are people who sell products to customers.
-
Logistics coordinators – They plan and coordinate logistics operations.
-
Purchasing agents are those who purchase goods and services for the company.
-
Customer service representatives - Answer calls and email from customers.
-
Shippers clerks - They process shipping order and issue bills.
-
Order fillers – They fill orders based upon what was ordered and shipped.
-
Quality control inspectors: They inspect outgoing and incoming products for any defects.
-
Others - There is a variety of other jobs in logistics. These include transportation supervisors and cargo specialists.
What are the main products of logistics?
Logistics refers to all activities that involve moving goods from A to B.
They include all aspects associated with transport including packaging, loading transporting, unloading storage, warehousing inventory management customer service, distribution returns and recycling.
Logisticians ensure the product reaches its destination in the most efficient manner. Logisticians assist companies in managing their supply chains by providing information such as demand forecasts, stock levels and production schedules.
They also keep track of shipments in transit, monitor quality standards, perform inventories and order replenishment, coordinate with suppliers and vendors, and provide support services for sales and marketing.
What does "warehouse" mean?
A warehouse is a place where goods are stored until they are sold. It can be an outdoor or indoor area. In some cases it could be both indoors and outdoors.
What are manufacturing & logistics?
Manufacturing refers to the process of making goods using raw materials and machines. Logistics manages all aspects of the supply chain, including procurement, production planning and distribution, inventory control, transportation, customer service, and transport. Sometimes manufacturing and logistics are combined to refer to a wider term that includes both the process of creating products as well as their delivery to customers.
Statistics
- Many factories witnessed a 30% increase in output due to the shift to electric motors. (en.wikipedia.org)
- (2:04) MTO is a production technique wherein products are customized according to customer specifications, and production only starts after an order is received. (oracle.com)
- It's estimated that 10.8% of the U.S. GDP in 2020 was contributed to manufacturing. (investopedia.com)
- Job #1 is delivering the ordered product according to specifications: color, size, brand, and quantity. (netsuite.com)
- You can multiply the result by 100 to get the total percent of monthly overhead. (investopedia.com)
External Links
How To
Six Sigma and Manufacturing
Six Sigma is "the application statistical process control (SPC), techniques for continuous improvement." Motorola's Quality Improvement Department, Tokyo, Japan, developed it in 1986. The basic idea behind Six Sigma is to improve quality by improving processes through standardization and eliminating defects. Since there are no perfect products, or services, this approach has been adopted by many companies over the years. Six Sigma's main objective is to reduce variations from the production average. This means that if you take a sample of your product, then measure its performance against the average, you can find out what percentage of the time the process deviates from the norm. If you notice a large deviation, then it is time to fix it.
Understanding how your business' variability is a key step towards Six Sigma implementation is the first. Once you understand this, you can then identify the causes of variation. Also, you will need to identify the sources of variation. Random variations occur when people make mistakes; systematic ones are caused by factors outside the process itself. If you make widgets and some of them end up on the assembly line, then those are considered random variations. But if you notice that every widget you make falls apart at the exact same place each time, this would indicate that there is a problem.
After identifying the problem areas, you will need to devise solutions. It might mean changing the way you do business or redesigning it entirely. You should then test the changes again after they have been implemented. If they don’t work, you’ll need to go back and rework the plan.