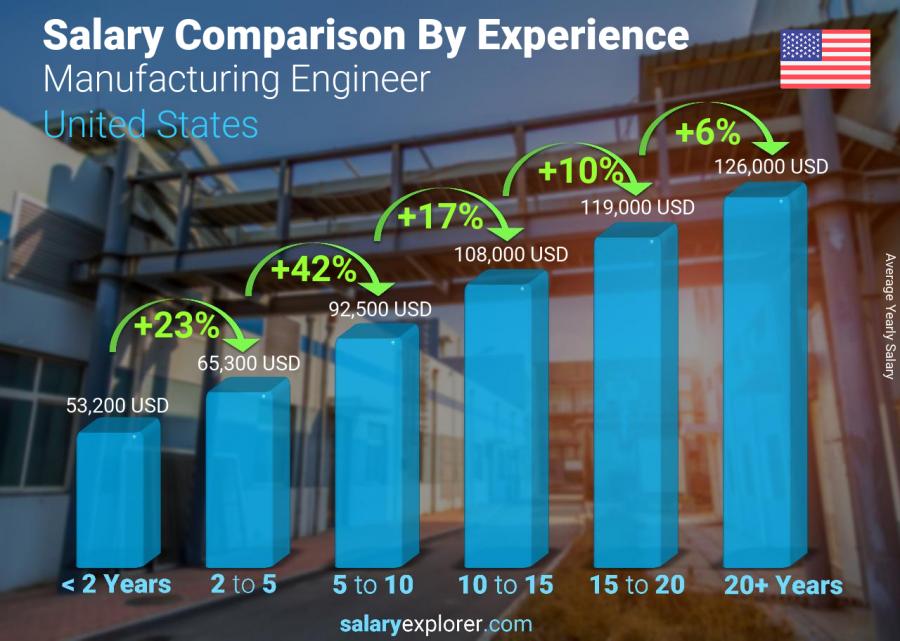
You will be an industrial designer and create innovative products for your home, office, or industry. You will learn about the job duties, the education and training required, and the expected salary. In addition, you'll discover how to get started in this field, and explore the various career paths available. Learn about the job's benefits and potential advancement. After you complete your education you can start your journey to a successful career as a designer.
Job duties
The Industrial Designer is responsible to design new products and services, integrating art, engineering, and business skills. They must ensure that brand strategies are aligned with their designs. To be a successful Industrial Designer, one must have experience in the field, and a strong portfolio of design concepts and designs brought to reality. Industrial Designers will need to have strong computer-aided software skills and be creative in incorporating innovative technology into products.
Industrial Designers develop and implement design regulations as part of the job. They must be analytically and problem-solving savvy and be able effectively communicate design concepts across functional teams. They need to be able and willing to collaborate with engineers, create CAD model, and work directly in model shops. Industrial Designers need to be proficient in Microsoft Office and Solidworks.
Education necessary
For those looking to work in this industry, a background in industrial design is a great asset. These programs allow students to create an electronic portfolio that showcases their design skills. Industrial designers may also be able to earn a Master of Business Administration degree. This helps them improve their business acumen as well as better understand the limitations of products. Industrial designers use their analytical skills to understand the needs of consumers and to develop innovative products and services.
The kind of work you are interested in is a factor in the education that an industrial designer needs. An industrial designer must hold at least an associate's degree. Some schools offer industrial design degrees. Others don't. Not only should candidates take courses on business and design but they also need to be able to study mathematics, computer science and engineering. Prospective employers will also appreciate a portfolio. Like all design jobs, there is a lot of career growth and advancement.
You have many career options
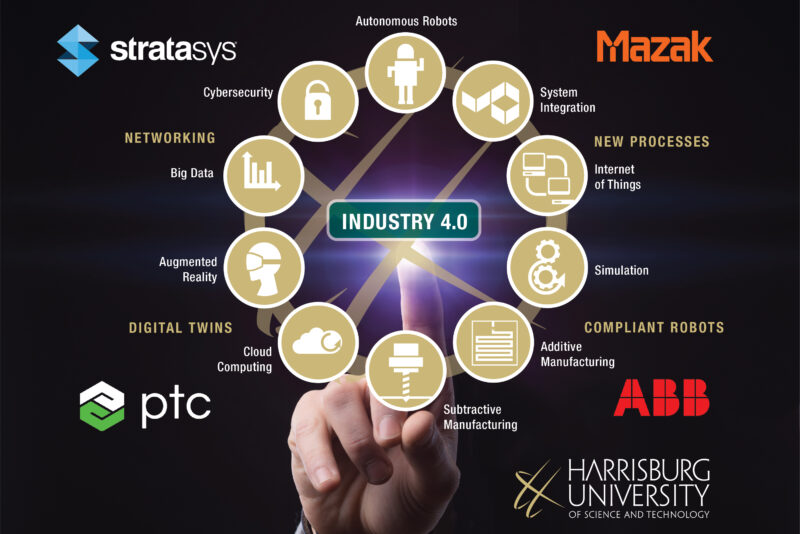
If you are interested to be an industrial designer, there are several entry-level job opportunities at design firms and manufacturing companies. Then, you can progress to more senior roles by applying for jobs as a chief designer or design department head. Any opportunity to improve your design skills is beneficial, regardless of the position you are interested in. Listed below are a few of the most common entry-level positions available to industrial designers.
An industrial designer usually has a bachelor's degree or related qualifications, and many employers look for candidates who have a background in graphics or sketching, as these skills can enhance their applications for jobs. In some instances, employers may prefer candidates with 3D modeling and CADD skills. A skilled industrial designer, whether you're an architect, civil engineer or engineer, will be needed to be able to draw, render, and present their work to decision makers.
Salary
The educational background and experience of industrial designers will impact the annual salary. A person who has a Masters or Doctorate degree in industrial design typically earns more that $75,019 per year. A Bachelor's degree pays less. Many industrial designers make it to management positions. Here are some tips for increasing your salary. First, read through the job description thoroughly and understand your exact salary expectations.
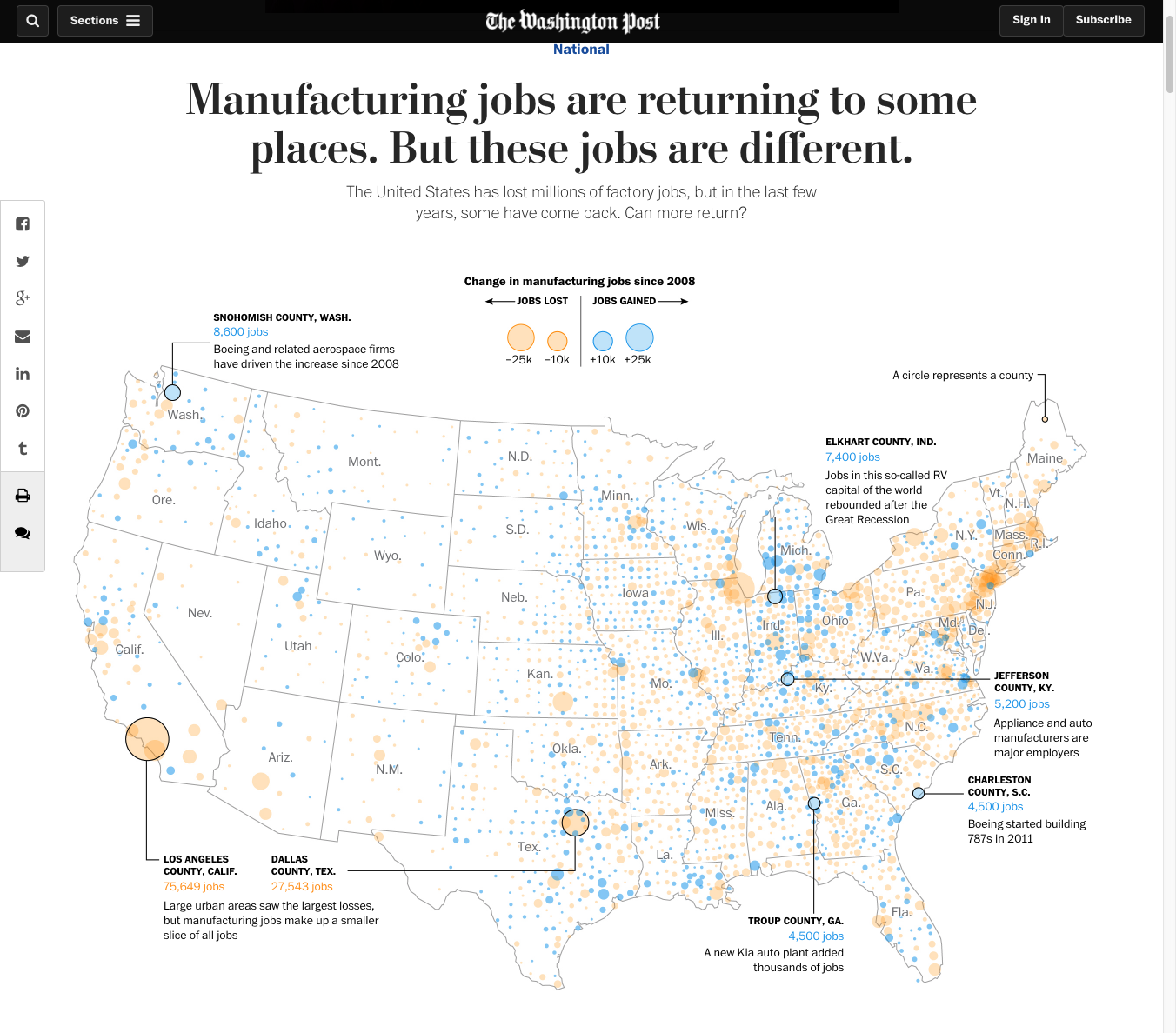
Industrial Designers earn an average annual salary of $62,315, though the actual amount can be much higher. The U.S. Bureau of Labor Statistics states that top earners are those who make more than $106,000 a year in this field. But, this is only an estimate. Your experience, industry, and work location will all impact your salary. After you have identified your skills and your location, you will want to examine the compensation for your industry.
FAQ
What are the responsibilities of a production planner
A production planner makes sure all project elements are delivered on schedule, within budget, as well as within the agreed scope. They also ensure the quality of the product and service meets the client's requirements.
How does manufacturing avoid bottlenecks in production?
Avoiding production bottlenecks is as simple as keeping all processes running smoothly, from the time an order is received until the product ships.
This includes planning for both capacity requirements and quality control measures.
This can be done by using continuous improvement techniques, such as Six Sigma.
Six Sigma is a management method that helps to improve quality and reduce waste.
It focuses on eliminating variation and creating consistency in your work.
What are the products of logistics?
Logistics are the activities involved in moving goods from point A to point B.
These include all aspects related to transport such as packaging, loading and transporting, storing, transporting, unloading and warehousing inventory management, customer service. Distribution, returns, recycling are some of the options.
Logisticians ensure that products reach the right destination at the right moment and under safe conditions. Logisticians assist companies in managing their supply chains by providing information such as demand forecasts, stock levels and production schedules.
They can also track shipments in transit and monitor quality standards.
What are the four types of manufacturing?
Manufacturing is the process that transforms raw materials into useful products. It can involve many activities like designing, manufacturing, testing packaging, shipping, selling and servicing.
Why automate your factory?
Modern warehousing is becoming more automated. E-commerce has brought increased demand for more efficient and quicker delivery times.
Warehouses should be able adapt quickly to new needs. Technology investment is necessary to enable warehouses to respond quickly to changing demands. The benefits of automating warehouses are numerous. These are just a few reasons to invest in automation.
-
Increases throughput/productivity
-
Reduces errors
-
Accuracy is improved
-
Safety enhancements
-
Eliminates bottlenecks
-
Companies can scale up more easily
-
Workers are more productive
-
The warehouse can be viewed from all angles.
-
Enhances customer experience
-
Improves employee satisfaction
-
Minimizes downtime and increases uptime
-
Ensures quality products are delivered on time
-
Removing human error
-
It ensures compliance with regulations
Statistics
- You can multiply the result by 100 to get the total percent of monthly overhead. (investopedia.com)
- Job #1 is delivering the ordered product according to specifications: color, size, brand, and quantity. (netsuite.com)
- In the United States, for example, manufacturing makes up 15% of the economic output. (twi-global.com)
- Many factories witnessed a 30% increase in output due to the shift to electric motors. (en.wikipedia.org)
- (2:04) MTO is a production technique wherein products are customized according to customer specifications, and production only starts after an order is received. (oracle.com)
External Links
How To
How to use lean manufacturing in the production of goods
Lean manufacturing is a management style that aims to increase efficiency and reduce waste through continuous improvement. It was created in Japan by Taiichi Ohno during the 1970s and 80s. He received the Toyota Production System award (TPS), from Kanji Toyoda, founder of TPS. Michael L. Watkins published the book "The Machine That Changed the World", which was the first to be published about lean manufacturing.
Lean manufacturing refers to a set of principles that improve the quality, speed and costs of products and services. It is about eliminating defects and waste from all stages of the value stream. Lean manufacturing can be described as just-in–time (JIT), total productive maintenance, zero defect (TPM), or even 5S. Lean manufacturing is about eliminating activities that do not add value, such as inspection, rework, and waiting.
Lean manufacturing improves product quality and costs. It also helps companies reach their goals quicker and decreases employee turnover. Lean manufacturing is considered one of the most effective ways to manage the entire value chain, including suppliers, customers, distributors, retailers, and employees. Lean manufacturing can be found in many industries. For example, Toyota's philosophy underpins its success in automobiles, electronics, appliances, healthcare, chemical engineering, aerospace, paper, food, etc.
Lean manufacturing includes five basic principles:
-
Define Value: Identify the social value of your business and what sets you apart.
-
Reduce Waste - Eliminate any activity that doesn't add value along the supply chain.
-
Create Flow. Ensure that your work is uninterrupted and flows seamlessly.
-
Standardize and Simplify – Make processes as consistent, repeatable, and as simple as possible.
-
Develop Relationships: Establish personal relationships both with internal and external stakeholders.
Lean manufacturing is not a new concept, but it has been gaining popularity over the last few years due to a renewed interest in the economy following the global financial crisis of 2008. Many businesses have adopted lean manufacturing techniques to help them become more competitive. Economists think that lean manufacturing is a crucial factor in economic recovery.
Lean manufacturing has many benefits in the automotive sector. These include higher customer satisfaction, lower inventory levels, lower operating expenses, greater productivity, and improved overall safety.
Any aspect of an enterprise can benefit from Lean manufacturing. Lean manufacturing is most useful in the production sector of an organisation because it ensures that each step in the value-chain is efficient and productive.
There are three types of lean manufacturing.
-
Just-in-Time Manufacturing (JIT): This type of lean manufacturing is commonly referred to as "pull systems." JIT refers to a system in which components are assembled at the point of use instead of being produced ahead of time. This method reduces lead times, increases availability, and decreases inventory.
-
Zero Defects Manufacturing (ZDM),: ZDM is a system that ensures no defective units are left the manufacturing facility. You should repair any part that needs to be repaired during an assembly line. This applies to finished products, which may need minor repairs before they are shipped.
-
Continuous Improvement (CI),: Continuous improvement aims improve the efficiency and effectiveness of operations by continuously identifying issues and making changes to reduce waste. Continuous improvement involves continuous improvement of processes and people as well as tools.