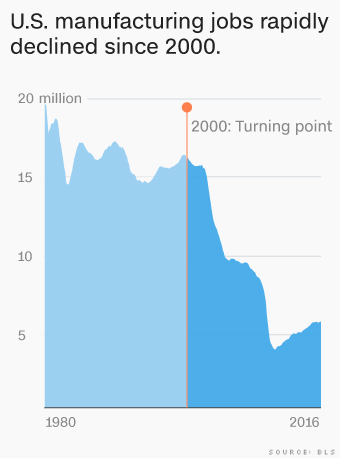
The United States is third in manufacturing in the world and saw its manufacturing output reach a record at $2.00 trillion in Q1 2018. This was nearly twice the amount it had before the Great Recession. However, despite a strong domestic economy, the United States manufacturing industry is taking a shotgun approach to its current challenges. This could be due to a shortage of skilled labor or investment, but we must be more aggressive in dealing with the problems facing our industry.
Since 2000, jobs have dropped by 5 million
Since 2000, the US has lost five millions manufacturing jobs. Although some believe that trade with China has contributed to the decrease in manufacturing jobs, this accounts for only a quarter of the total decline. Manufacturing jobs were also lost in countries that couldn't compete with Chinese imports. But there are many factors that contributed to the decline of manufacturing jobs. The following are some of the reasons:
During the last two decades, the US manufacturing sector lost nearly a third of its jobs. It was 17,000,000 in 1965. It dropped to just 12,000,000 in 2010. While the decline in manufacturing jobs is not the fault of trade, it has been the result of structural problems - a decline in capital investment, output, productivity, and trade deficits - which are not sustainable. Although productivity gains played a significant role in the decline of manufacturing jobs, they were not enough to compensate. Automation is the problem, and not productivity improvements.
Strong demand for manufactured goods
In the United States, the demand for manufactured goods remains strong despite the fact that the share of consumer spending on these items has decreased over the past few decades. In 1945, 58% of personal spending on durable goods was made, while it is now only 28%. This is because the costs of manufacturing and selling durable goods have dropped, while the contents have increased. This has led to a significant drop in the price of computers, TVs, and audio equipment.
The US has seen a rise in manufacturing activity, which has led to an increase in production. According to the Fifth District Manufacturing Activity Survey, demand is high for manufactured goods and production is increasing. However, supply chain bottlenecks are limiting output. Increased production has put pressure on supply chains. Many respondents reported experiencing supply chain disruptions that have affected their ability to keep necessary inventories. Backlogs and lead times for vendors have increased.
In the last decade, the trade deficit in manufactured goods has more that doubled
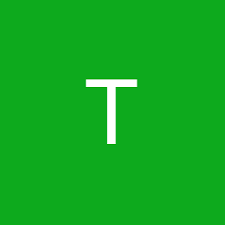
Some economists worry that the U.S.'s trade surplus will lower global growth and create more instability among its trading partners. Others point out that high imports of US manufactured goods are not necessarily a bad thing for the U.S. economy, which is a key to maintaining global economic stability. Trade deficits may be an inevitable evil since the U.S. is heavily dependent on foreign markets to generate its economy. This may make it more difficult to achieve full employment.
The U.S. trade deficit with China in manufactured goods has almost doubled since 2000. The increase in Chinese imports is partially responsible for the growing US deficit. This imbalance is mainly concentrated in the manufacturing sector. Wages and employment have fallen since the 1990s, which is the bigger problem. US manufacturing employment fell dramatically from 26% in 1970 to 8.5% in 2016. Some economists attribute the decline to China's increased competition, but most attribute the decline to automation, productivity increases, and demand shifting away from goods to services.
Industry has a shotgun approach
The US has a variety of advanced manufacturing initiatives. It is also well-established in this area. But some countries are attempting to introduce the internet of things to manufacturing. The US, however, is a multi-technology nation that combines traditional mass media with Internet advertising. The result is a shotgun approach. Companies focus on many technologies and target a broad client base.
FAQ
What are the logistics products?
Logistics refers to the movement of goods from one place to another.
They cover all aspects of transportation, such as packing, loading, transporting and unloading.
Logisticians make sure that the right product arrives at the right place at the correct time and in safe conditions. They provide information on demand forecasts as well stock levels, production schedules and availability of raw material.
They monitor shipments in transit, ensure quality standards, manage inventories, replenish orders, coordinate with suppliers and other vendors, and offer support services for sales, marketing, and customer service.
What are the 7 Rs of logistics management?
The acronym 7Rs of Logistics refers to the seven core principles of logistics management. It was developed and published by the International Association of Business Logisticians in 2004 as part of the "Seven Principles of Logistics Management".
The following letters make up the acronym:
-
Responsive - ensure all actions are legal and not harmful to others.
-
Reliable - You can have confidence that you will fulfill your promises.
-
It is reasonable to use resources efficiently and not waste them.
-
Realistic – Consider all aspects, including cost-effectiveness as well as environmental impact.
-
Respectful - treat people fairly and equitably.
-
Reliable - Find ways to save money and increase your productivity.
-
Recognizable: Provide customers with value-added service
Are there any Manufacturing Processes that we should know before we can learn about Logistics?
No. No. It is important to know about the manufacturing processes in order to understand how logistics works.
What is the distinction between Production Planning or Scheduling?
Production Planning (PP), is the process of deciding what production needs to take place at any given time. This is accomplished by forecasting the demand and identifying production resources.
Scheduling is the process of assigning specific dates to tasks so they can be completed within the specified timeframe.
How can manufacturing avoid production bottlenecks
Avoiding production bottlenecks is as simple as keeping all processes running smoothly, from the time an order is received until the product ships.
This includes both quality control and capacity planning.
This can be done by using continuous improvement techniques, such as Six Sigma.
Six Sigma is a management method that helps to improve quality and reduce waste.
It emphasizes consistency and eliminating variance in your work.
Statistics
- Many factories witnessed a 30% increase in output due to the shift to electric motors. (en.wikipedia.org)
- In 2021, an estimated 12.1 million Americans work in the manufacturing sector.6 (investopedia.com)
- According to the United Nations Industrial Development Organization (UNIDO), China is the top manufacturer worldwide by 2019 output, producing 28.7% of the total global manufacturing output, followed by the United States, Japan, Germany, and India.[52][53] (en.wikipedia.org)
- (2:04) MTO is a production technique wherein products are customized according to customer specifications, and production only starts after an order is received. (oracle.com)
- Job #1 is delivering the ordered product according to specifications: color, size, brand, and quantity. (netsuite.com)
External Links
How To
Six Sigma in Manufacturing
Six Sigma is "the application statistical process control (SPC), techniques for continuous improvement." It was developed by Motorola's Quality Improvement Department at their plant in Tokyo, Japan, in 1986. Six Sigma's main goal is to improve process quality by standardizing processes and eliminating defects. Since there are no perfect products, or services, this approach has been adopted by many companies over the years. Six Sigma's primary goal is to reduce variation from the average value of production. You can calculate the percentage of deviation from the norm by taking a sample of your product and comparing it to the average. If it is too large, it means that there are problems.
Understanding the nature of variability in your business is the first step to Six Sigma. Once you have this understanding, you will need to identify sources and causes of variation. You'll also want to determine whether these variations are random or systematic. Random variations occur when people do mistakes. Symmetrical variations are caused due to factors beyond the process. You could consider random variations if some widgets fall off the assembly lines. However, if you notice that every time you assemble a widget, it always falls apart at exactly the same place, then that would be a systematic problem.
Once you have identified the problem, you can design solutions. It might mean changing the way you do business or redesigning it entirely. Test them again once you've implemented the changes. If they don’t work, you’ll need to go back and rework the plan.